The watch brand Armin Strom puts a lot of attention to the visibility of the movement as it is the driving engine and highly complex mechanism that keeps the watch running. Therefore they specialized in skeletonized movement designs to bring the inside to the outside for its wearer. Most people cannot imagine how intense work needs to be done to put all bits and pieces together until a watch is actually running.
The Armin Strom manufacture – which was founded by Serge Michel and Claude Greisler in 2008 to continue the work of watchmaker Armin Strom – is a wonderful place where all this happens under one roof on a manageable area. As they only produce a limited amount of watches per year the manufacture is not spacious like that of other watch brands, but fully equipped with everything that is necessary to produce a mechanical watch.

The Armin Strom Manufacture in Biel / Bienne
The Armin Strom manufacture is not dependent on the quality and availability of products by external suppliers as (almost) every piece is produced in-house. We had the pleasure to have an exclusive insight into the manufacture in Biel and follow them through all necessary steps from design to fabrication, decoration and assembling of their watches. Each step is a horological journey for itself and we are happy to share our impressions with you.
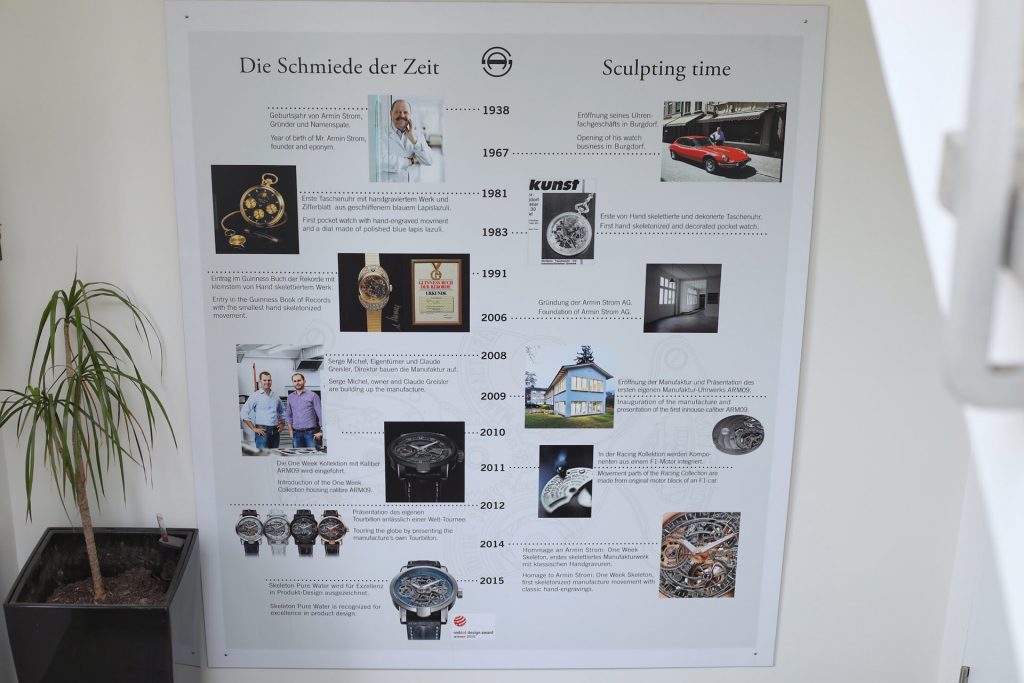
Sculpting time – Armin Strom from 1938 to 2015 at a glance
Design
At the very start the idea of a timepiece has to be put on paper. Which functions should the watch have except showing the time? How small or big should it be? How much power needs to be put on the escapement so the balance spring can turn in the right amplitude? And so on…
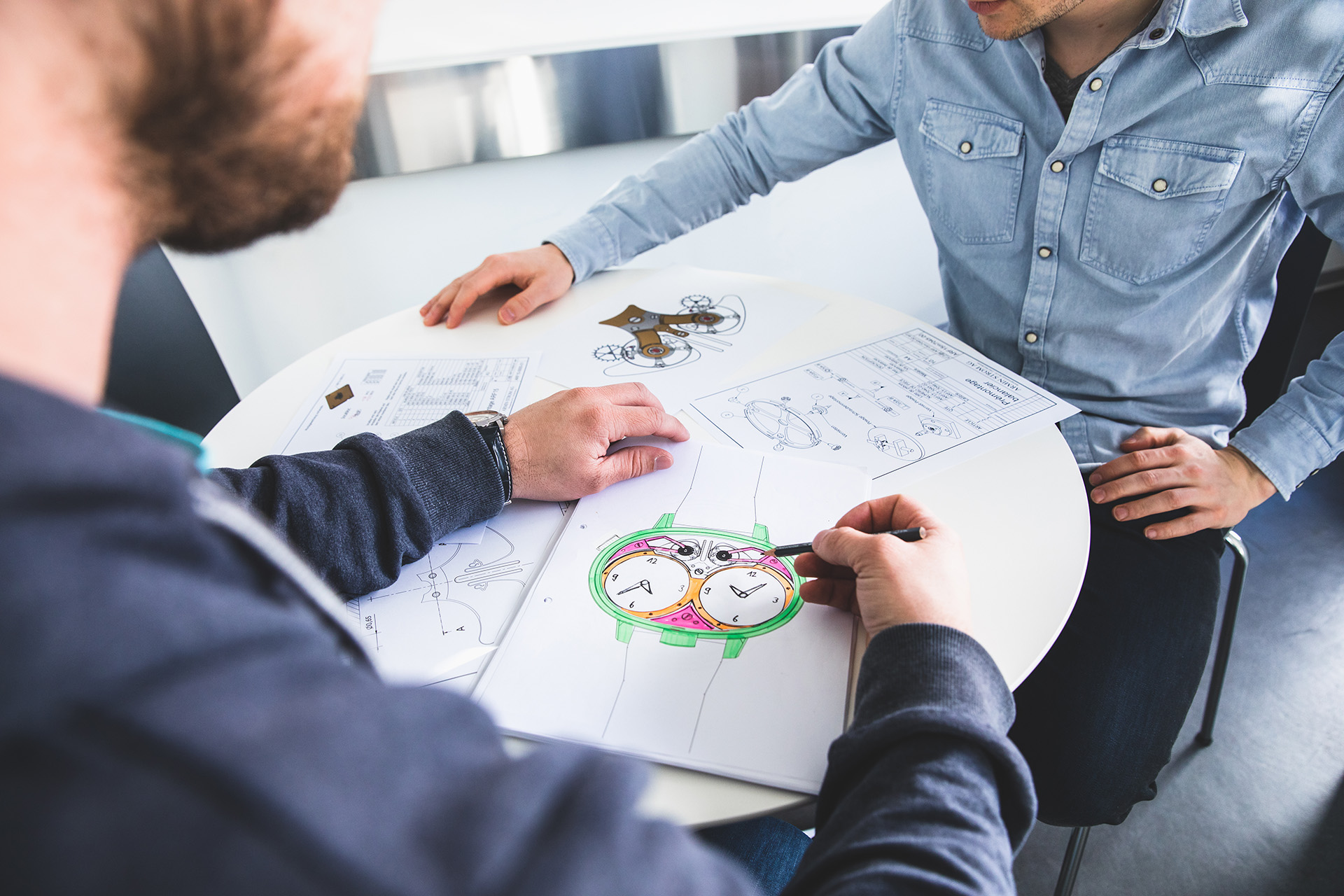
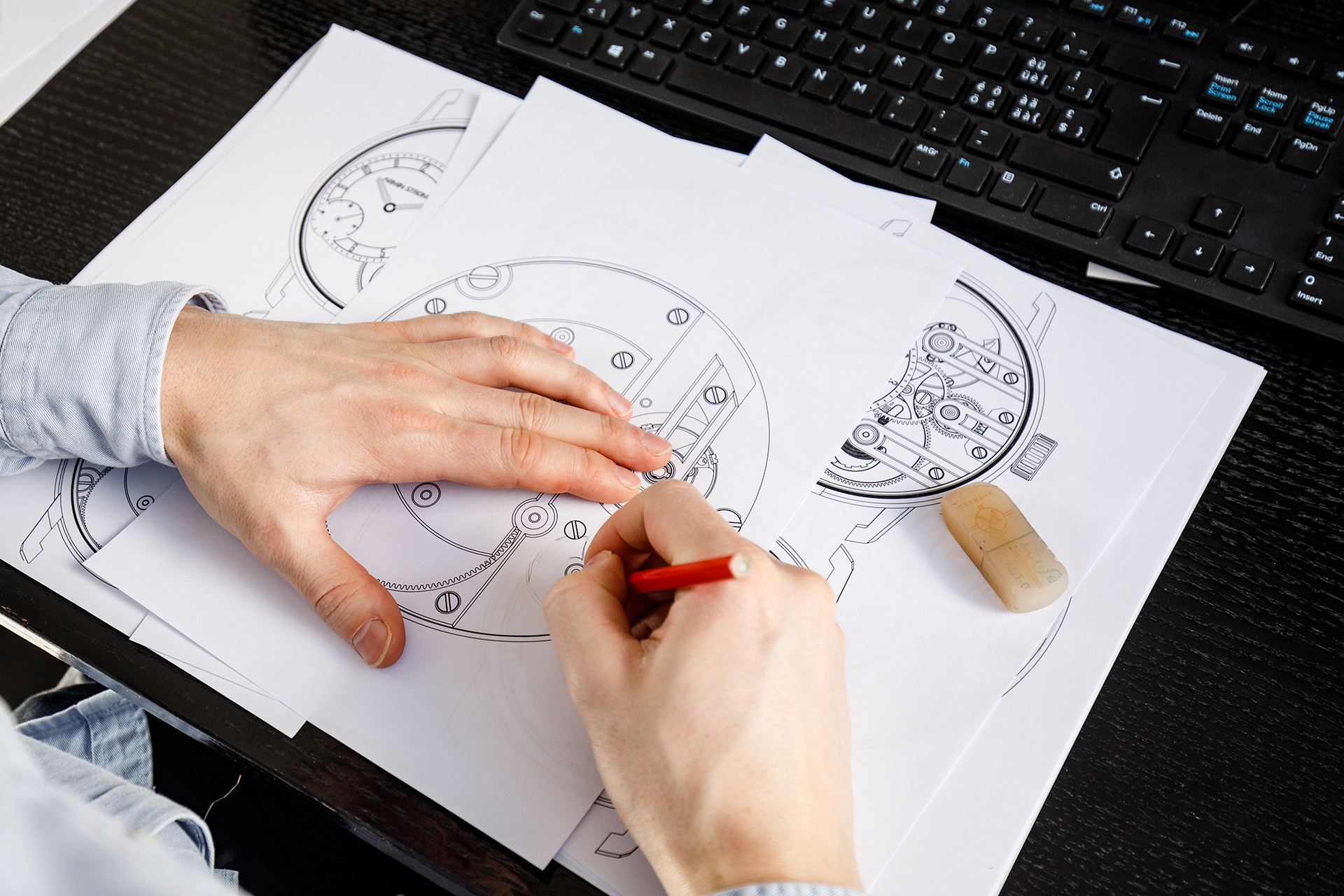
Bear in mind that there are a few hundred pieces in each movement that all want to be taken care of equally. So the creative minds undergo some extensive calculations and sketching to solve the puzzle, which is then feed into a computer simulation tool. Thankfully this is possible nowadays as it shows exactly how plates and bridges need to be milled and drilled from a solid piece of brass. For the skeletonizing process of the movement, all material that is not essential for the mechanical stability of the watch is also mechanically and accurately removed from plates and bridges. Already in this step design and fabrication work closely together.
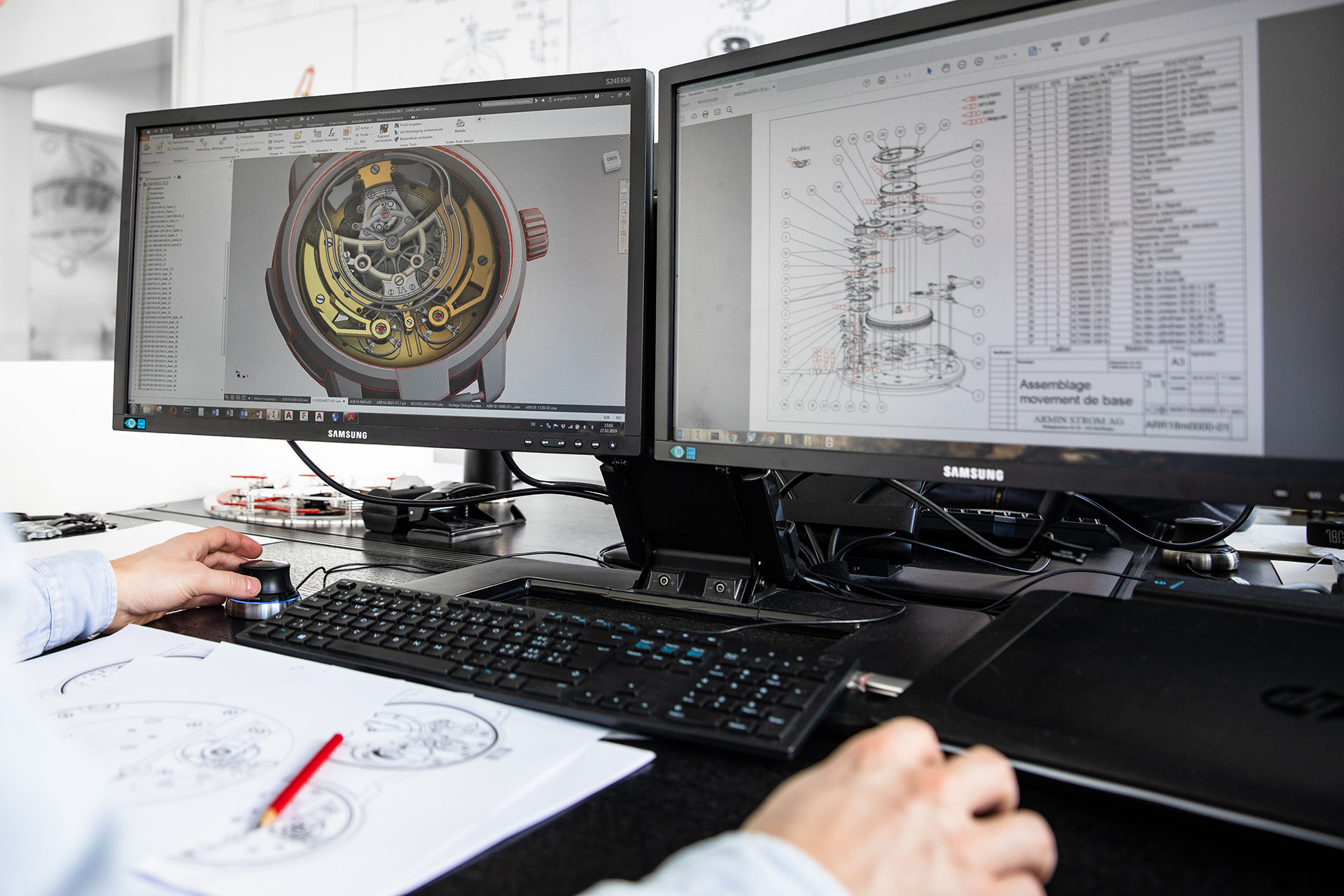
Each of the around 300 to 500 pieces of a watch need to be sketched and put in place first
Fabrication
Once all the data is checked on possible mistakes and being approved, the plates, bridges, wheels, levers, springs and screws are manufactured in-house. Armin Strom is able to control all manufacturing processes (with a few exceptions) from raw material to end product. Also, all parts are drilled, milled, turned and wire-eroded but never stamped as stamping might have a negative impact on the material structure. By this more complex method Armin Strom can work the tiny pieces with an accuracy of up to one hundredth of a millimetre.
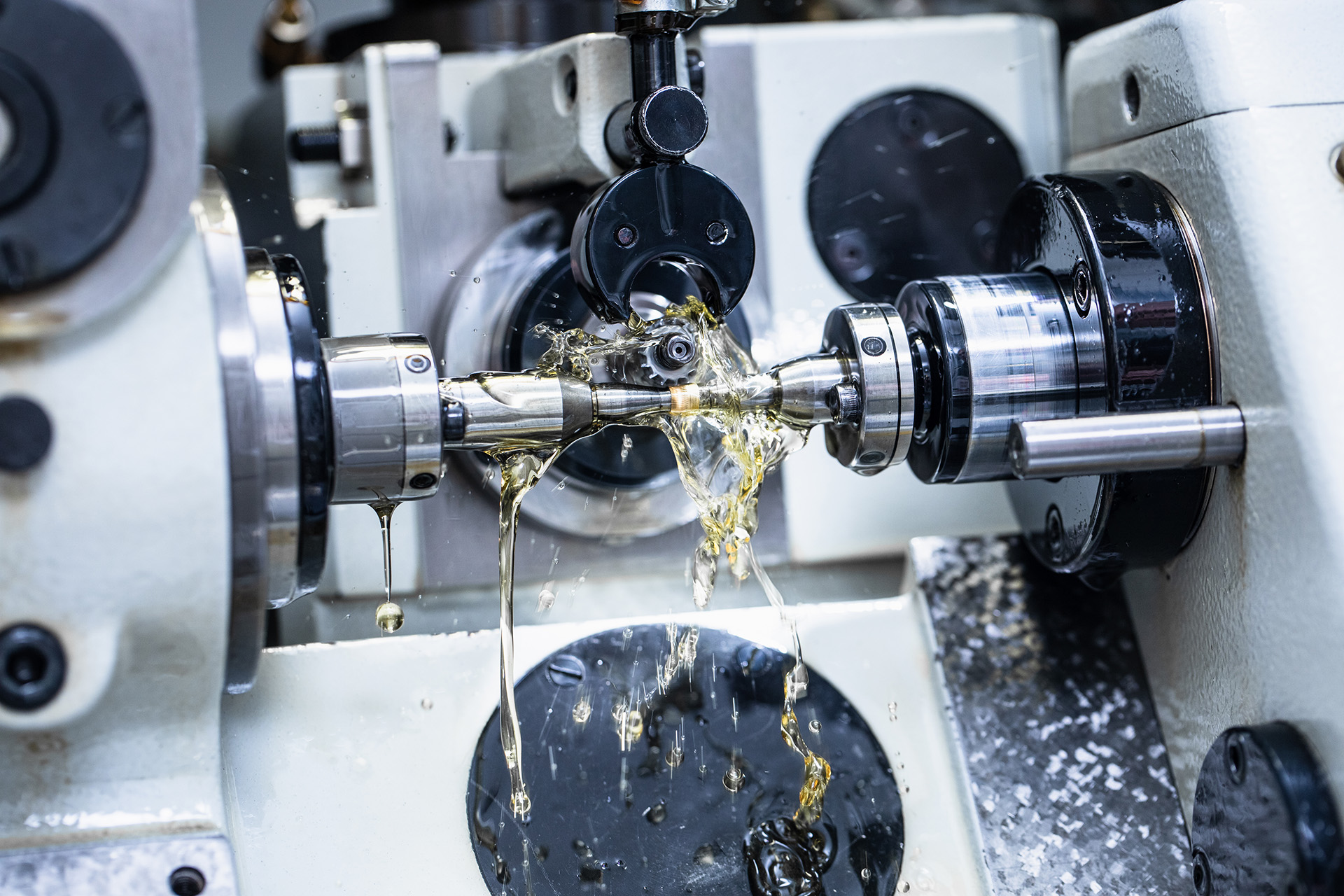
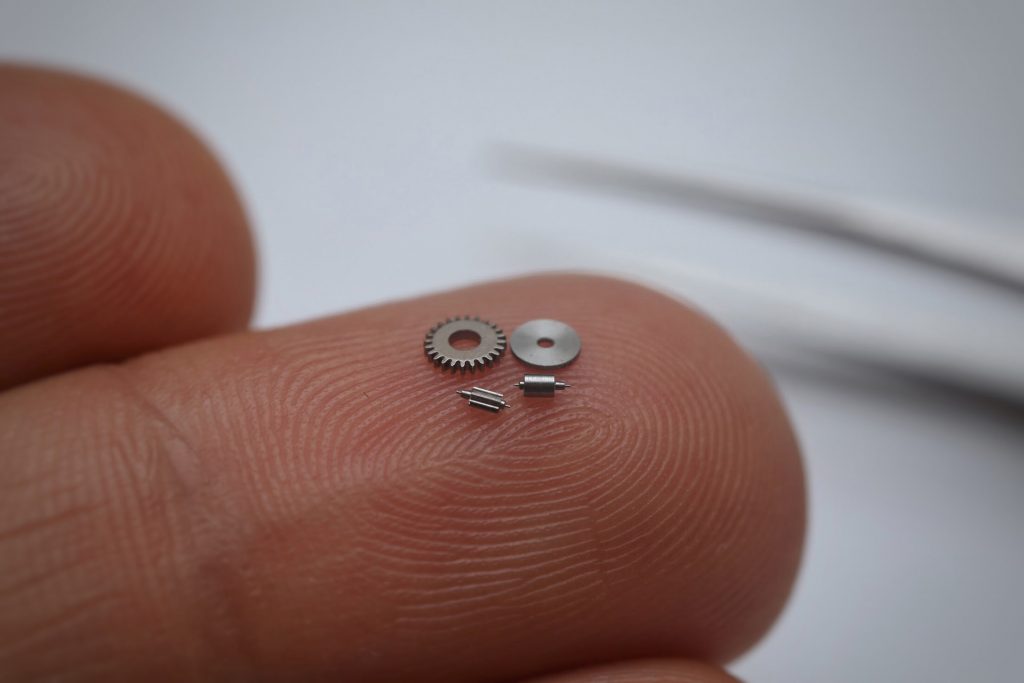
After manufacturing every piece needs to undergo a final control to check that everything matches with the calculations made.
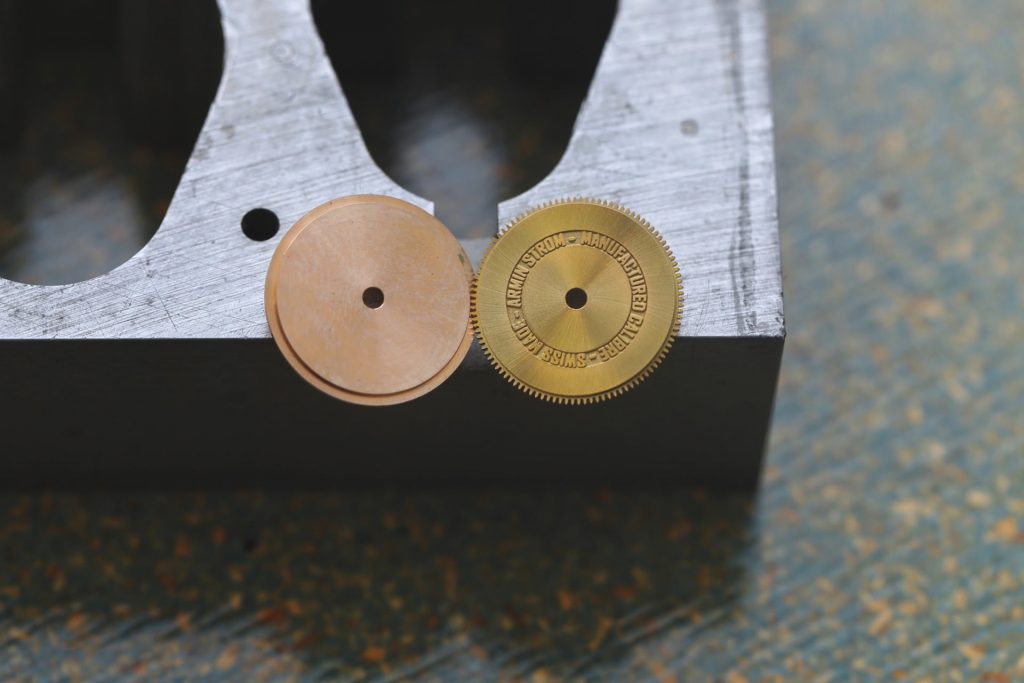
At the Armin Strom Manufacture pieces are being drilled and milled but never stamped
Decoration
Until now all individual parts are identically. Only now, the decoration part makes every piece unique. In the Armin Strom Manufacture you will find all sorts of new and traditional machines that enable a 360 degree decoration service and proves the mastery of Haute Horlogerie. The engraver works by hand and of course cannot work as precise as a machine would. Working on bare brass or steel is a Sisyphean task and after decoration, all parts need to be polished. Even for a small part like a pallets bridge a watchmaker needs to spend around half an hour on chamfering and polishing edges. Every part is polished even if it is in the end not visible in the finished watch.
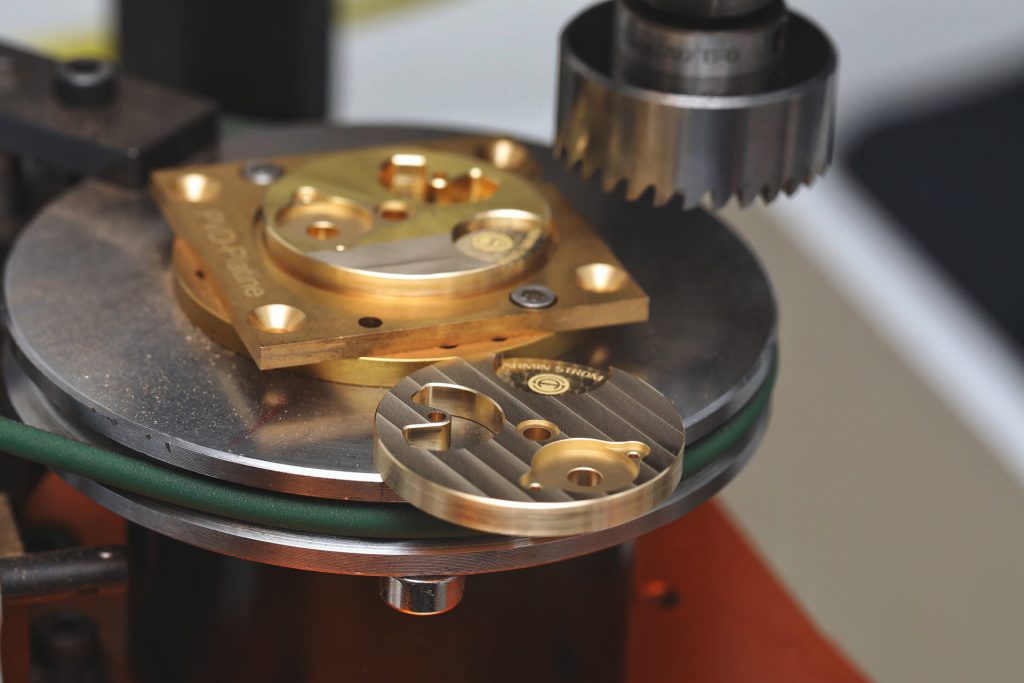
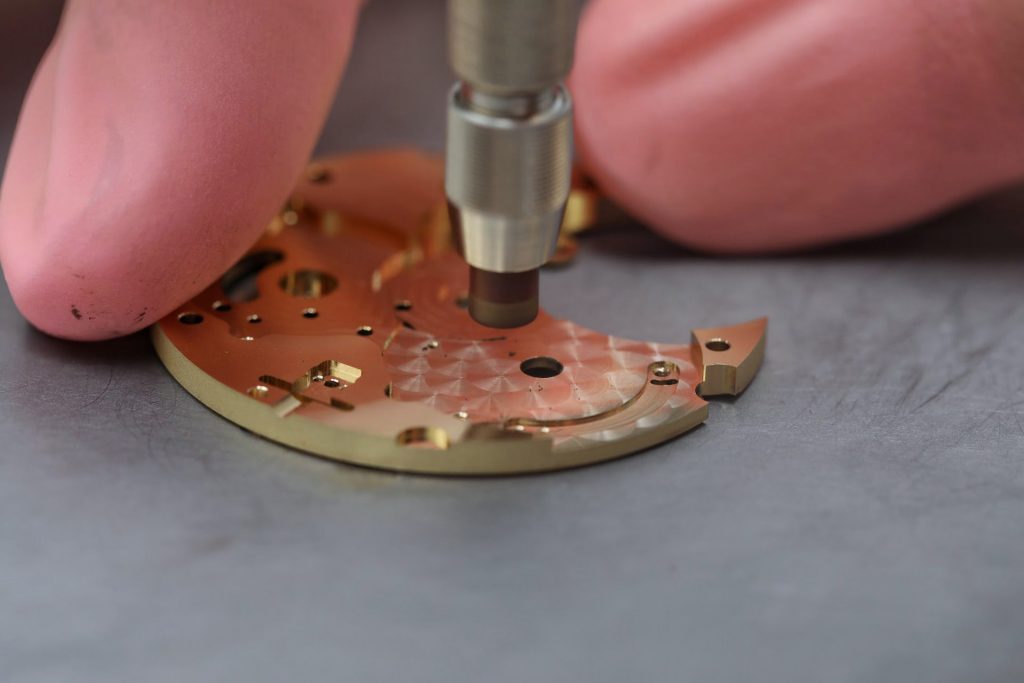
Geneva Stripes (left)
‘Perlage’ (right)
Another part of the Haute Horlogerie is the ‘Perlage’, a circular graining method generally used on the main plate. The watchmaker uses a rotating pencil, which is gently moved in a circular manner across the surface and creates these cloudy-looking, overlapping motives. At the very end the workpieces are given a ‘Geneva Stripes’ finish.
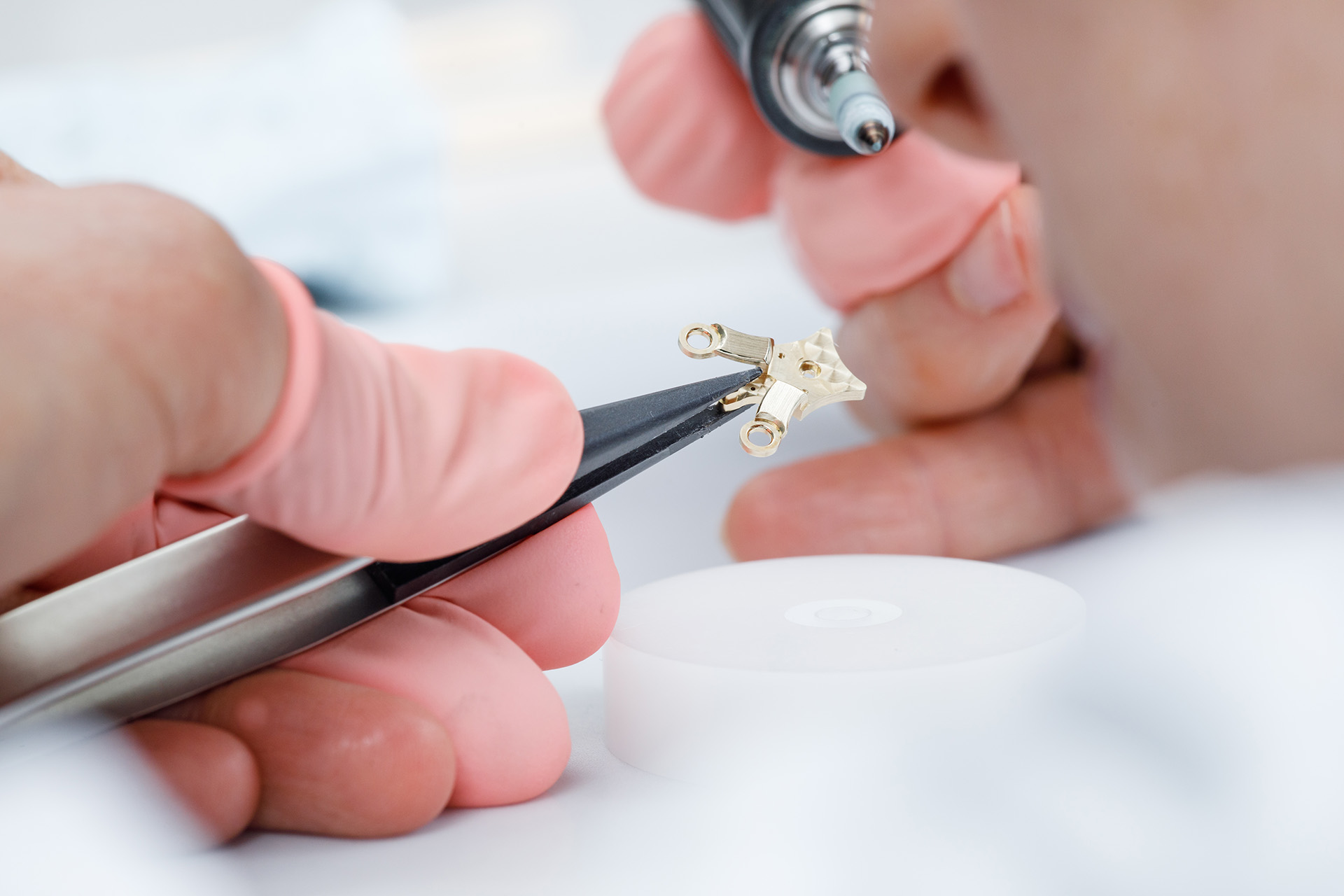
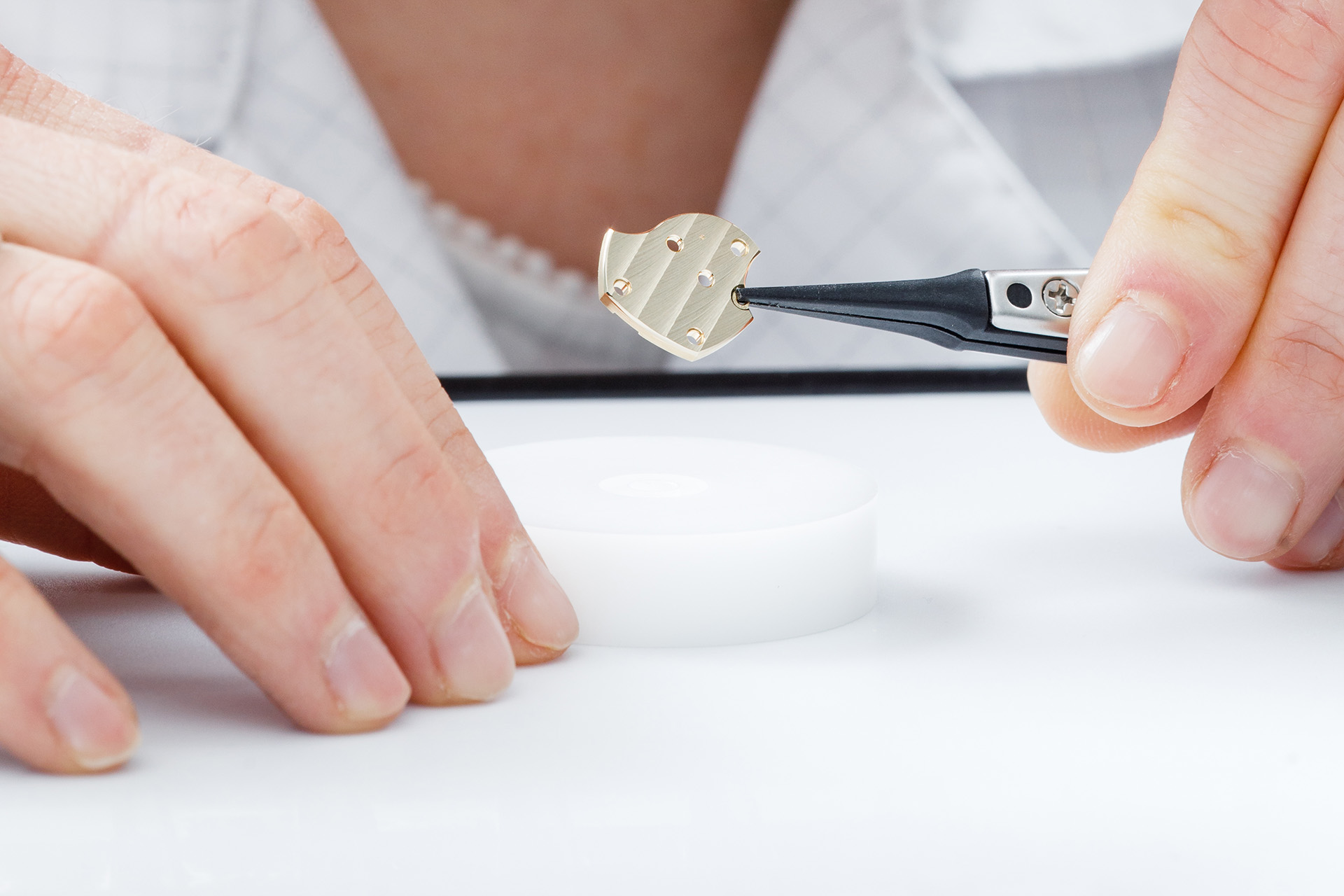
Electroplating
Now it’s time for a bath. Once decorated and polished, the individual parts (mainly bridges, plates, wheels and levers) are diving into a plating bath, the process called electroplating. All steel and brass parts are coated with pre-gold and then with a layer of nickel. Nickel protects against corrosion and hardens the surface. In a second step the plates – depending on the model and style of the watch – take another bath and are coated with either yellow-or rose gold, whereas the bridges are coated with a shining white rhodium.
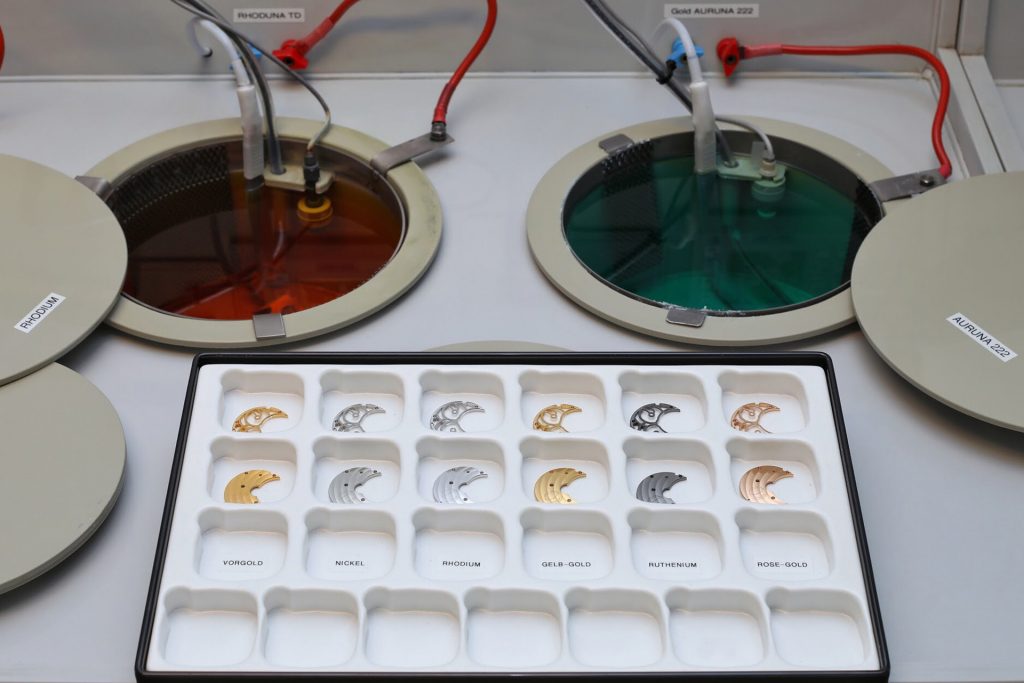
The plating bath strengthens the plates and gives them the shiny finish
Assembling
In a final step the watch is coming alive. But it is not just done by simply putting all pieces together. It’s a crucial operation – the watchmaker uses a pressing tool to insert the jewel bearings for the spindles of the toothed wheels into the plate and bridges. The way the jewels are pressed in influences the correct vertical play of the gear-train. Only now all remaining movement-parts can go into position. But as if it was not already laborious enough, the movement is completely disassembled again.
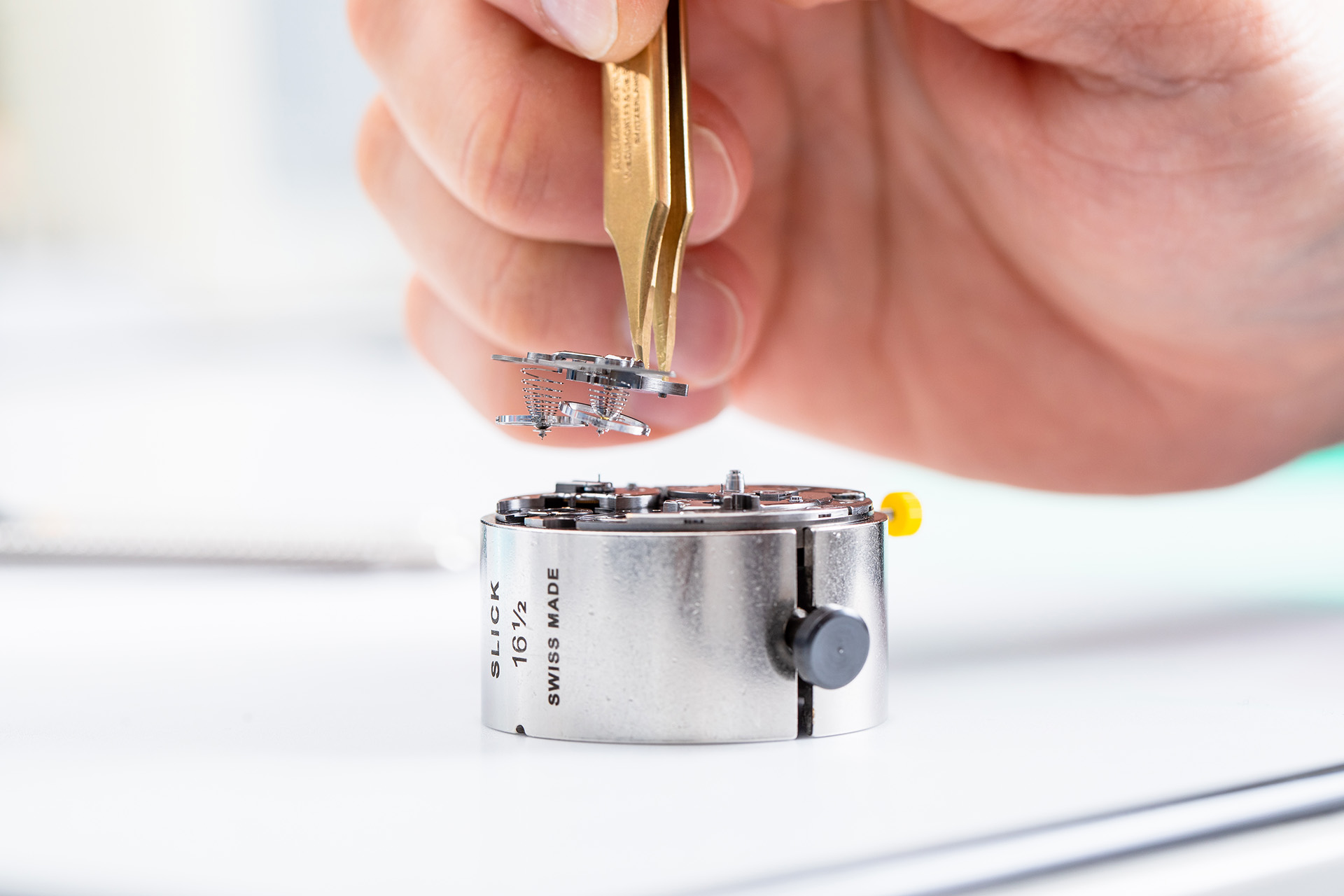
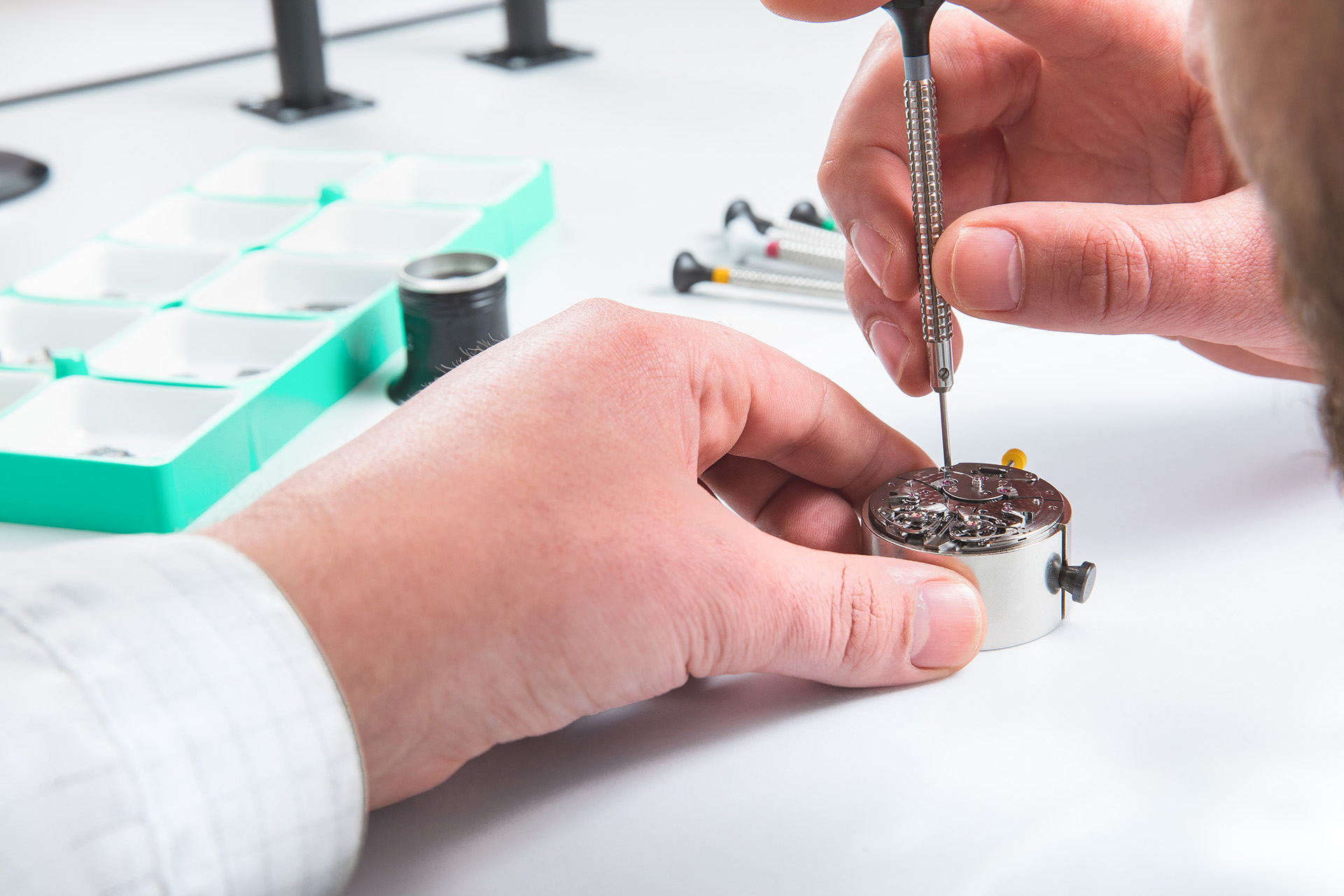
All parts need to be washed and dried before they can go back in place and receive some lubrication. After another few days of testing phase and only when the watch has passed all the quality tests it is finally ready for the customer.
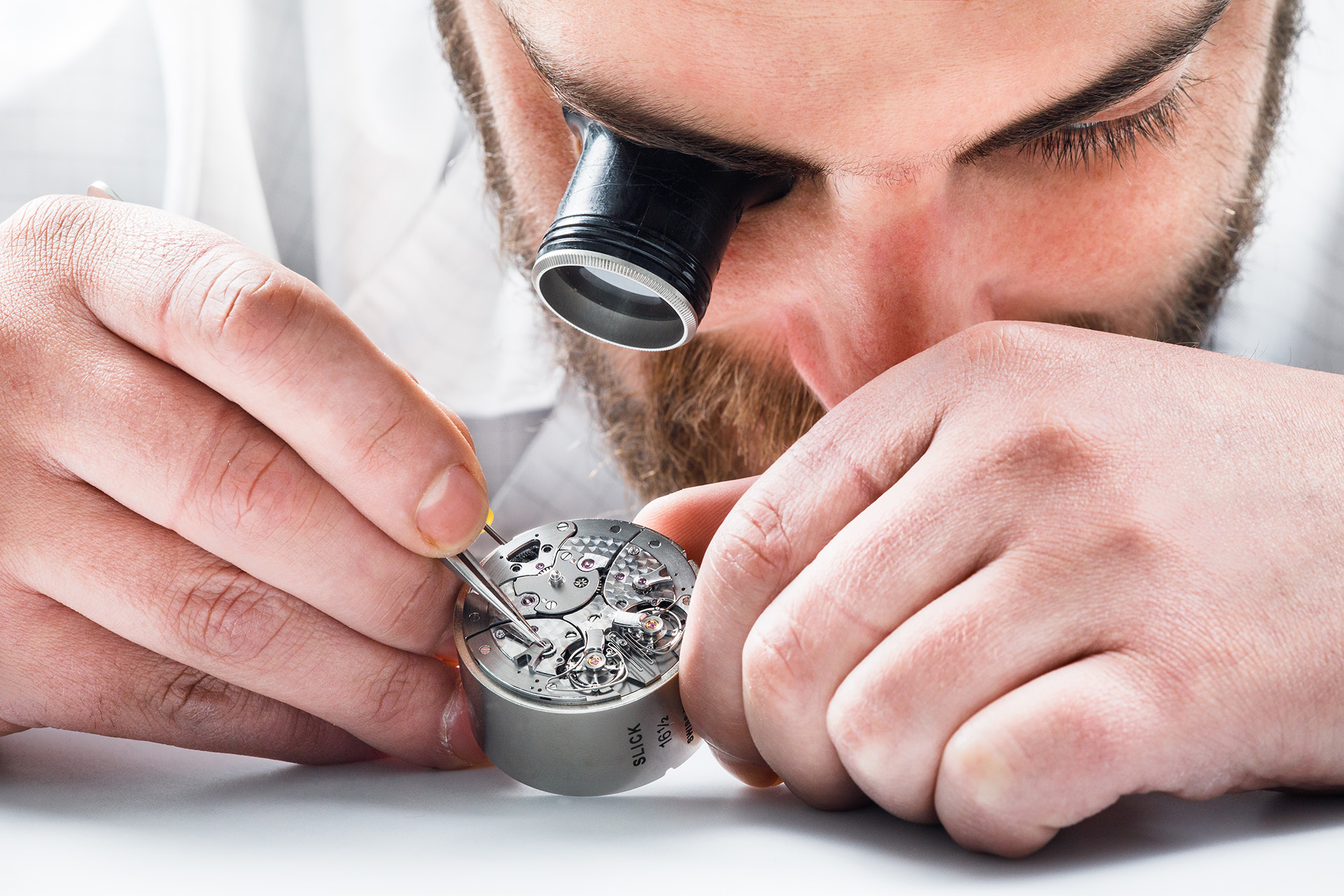
The final step – the assembling of the movement
Gallery

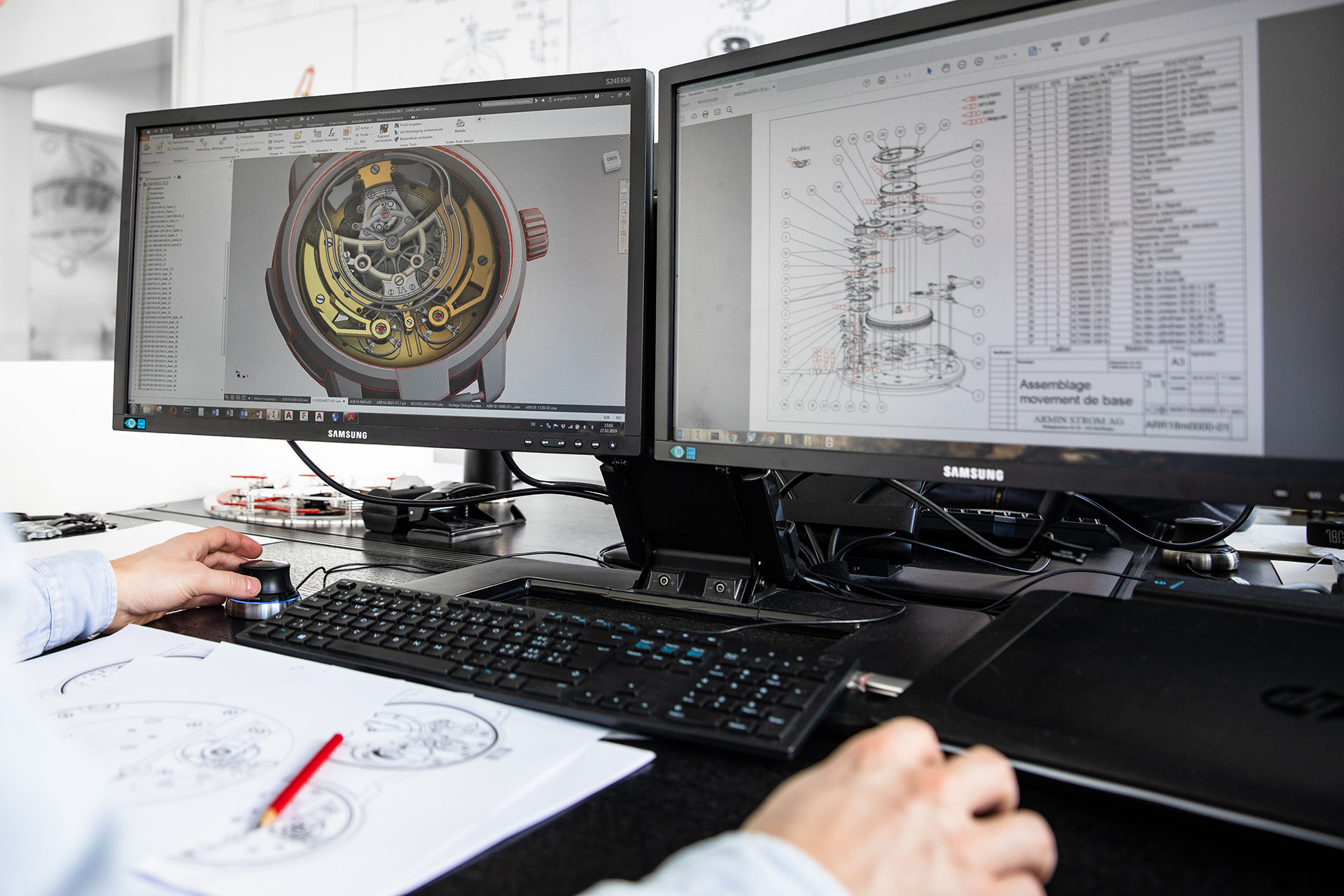
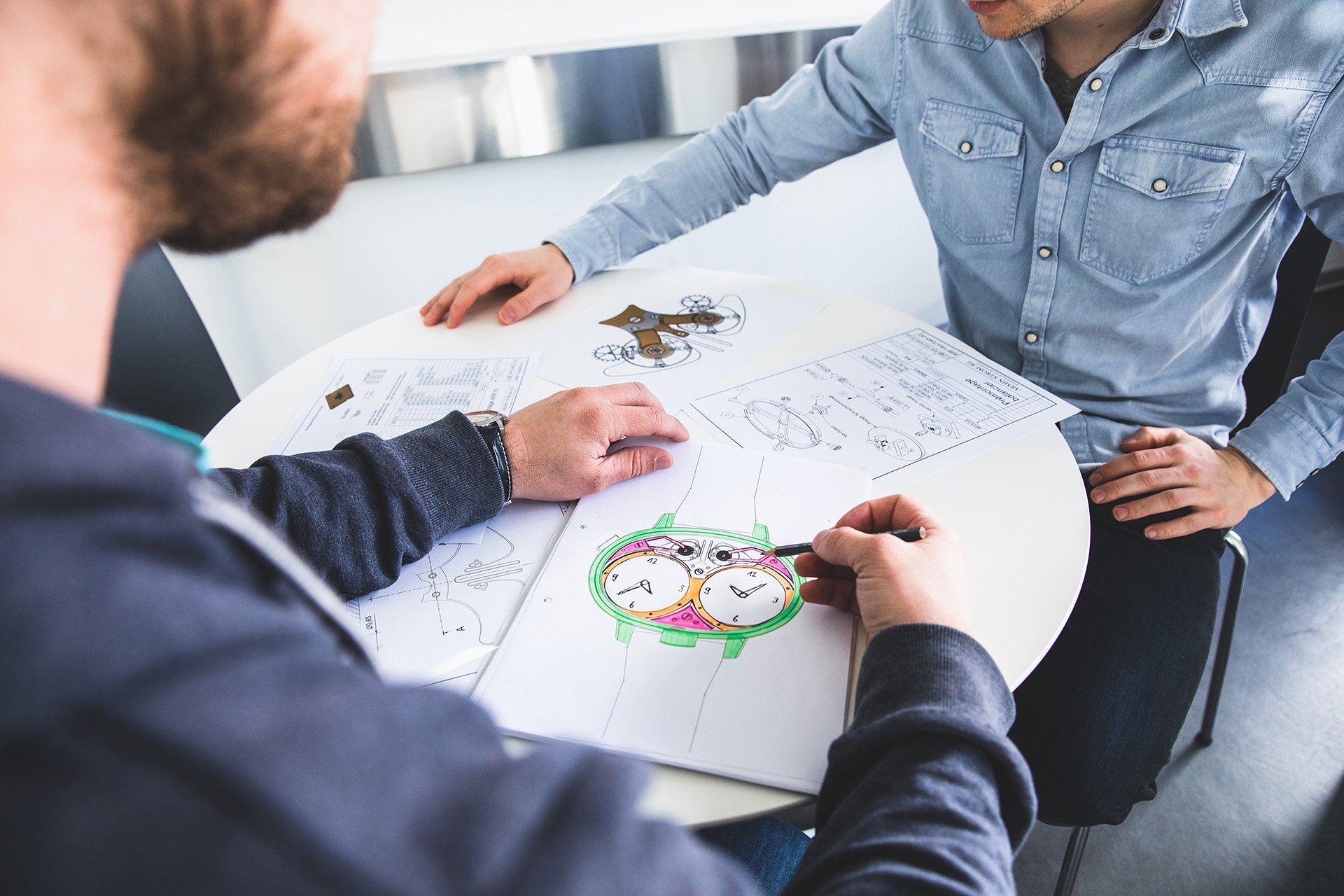
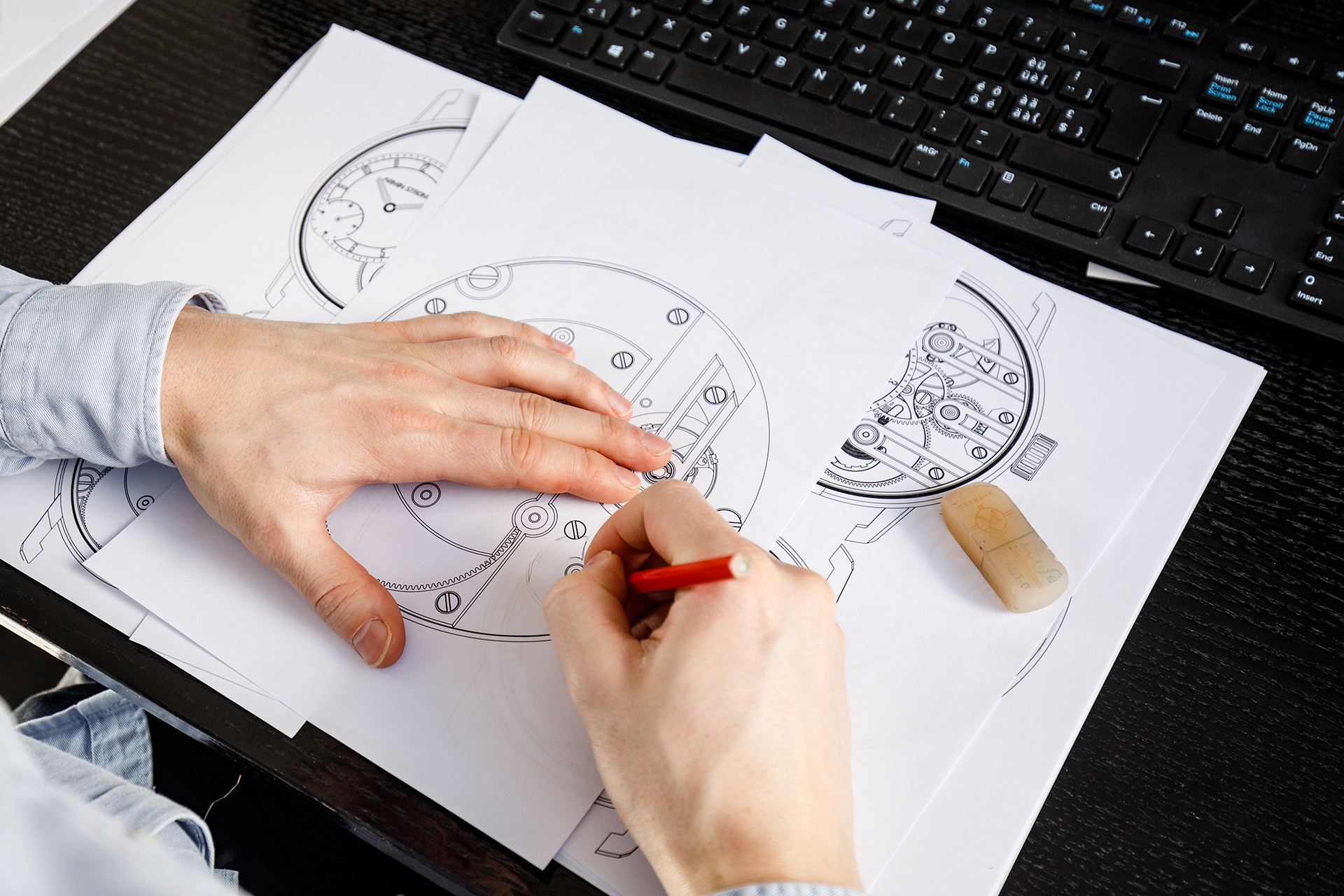
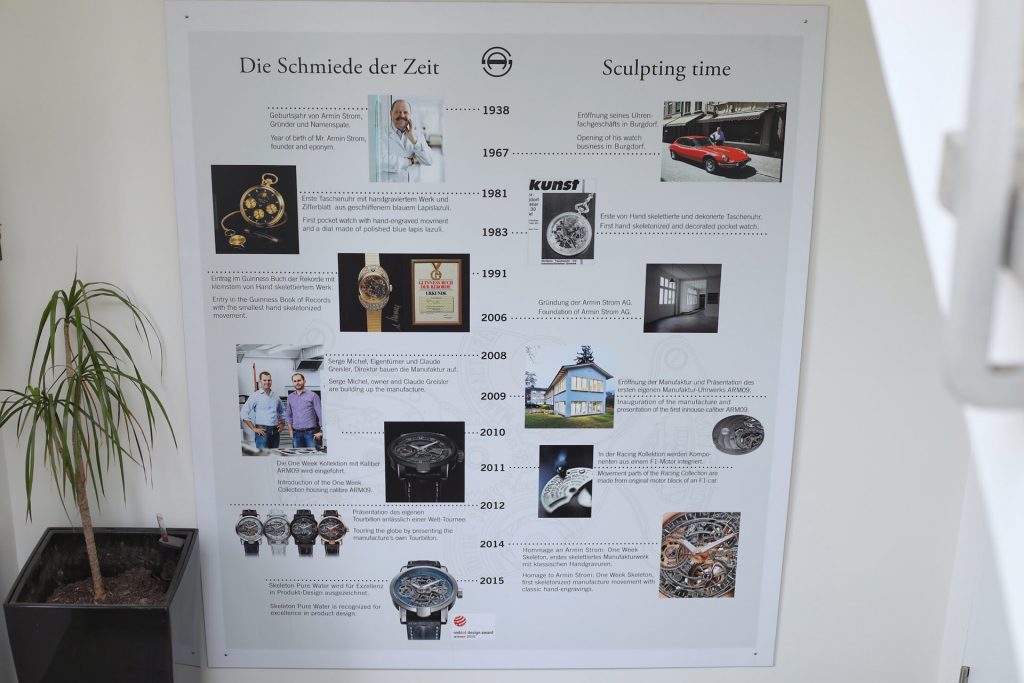
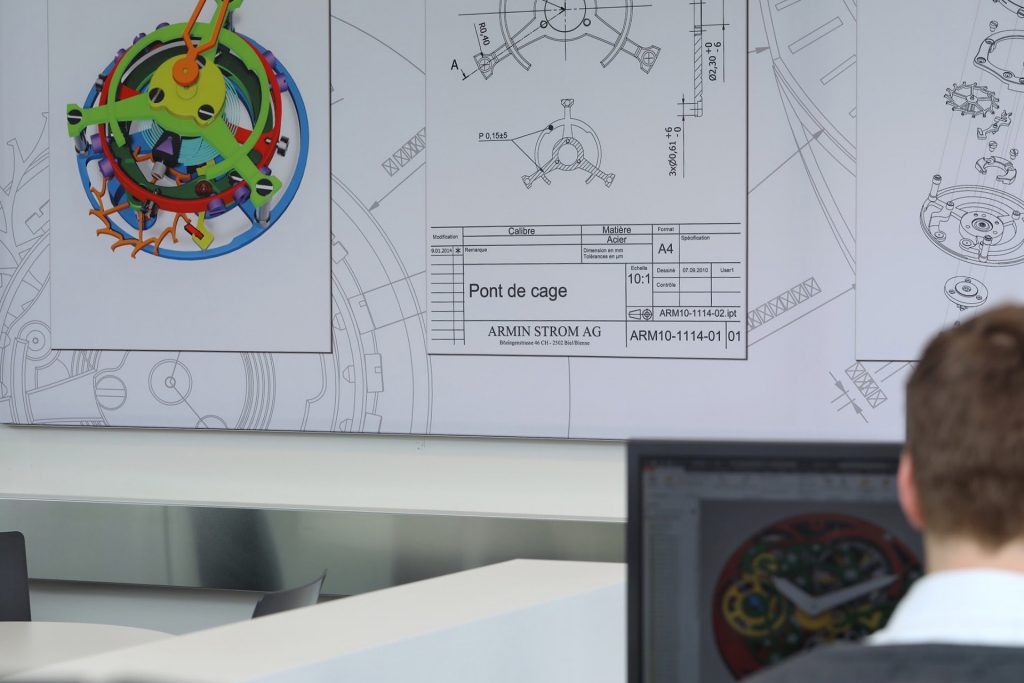
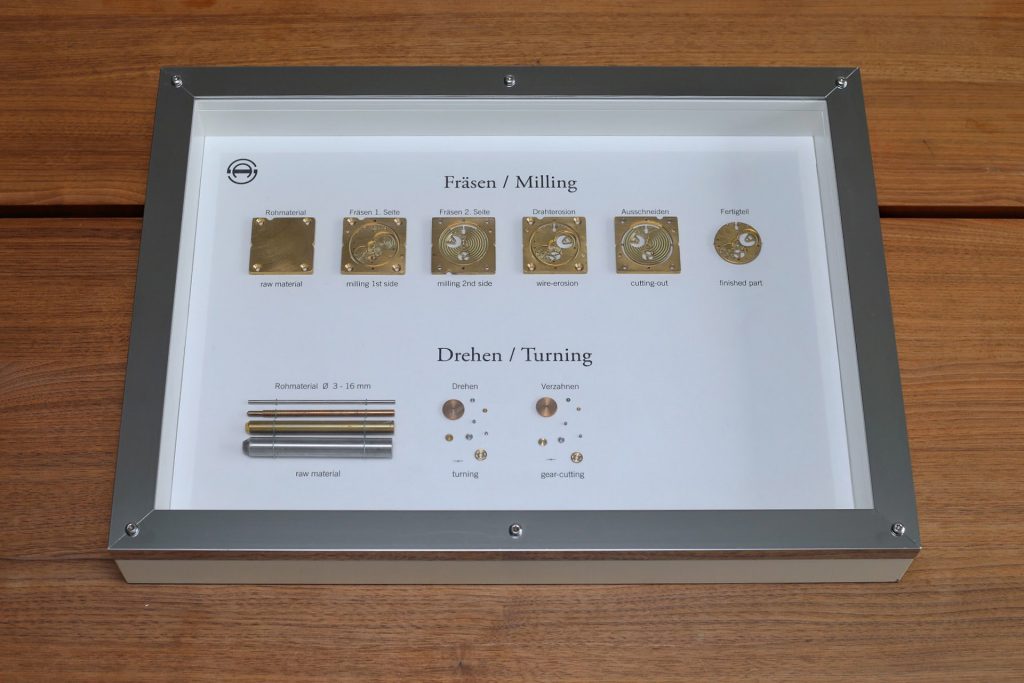
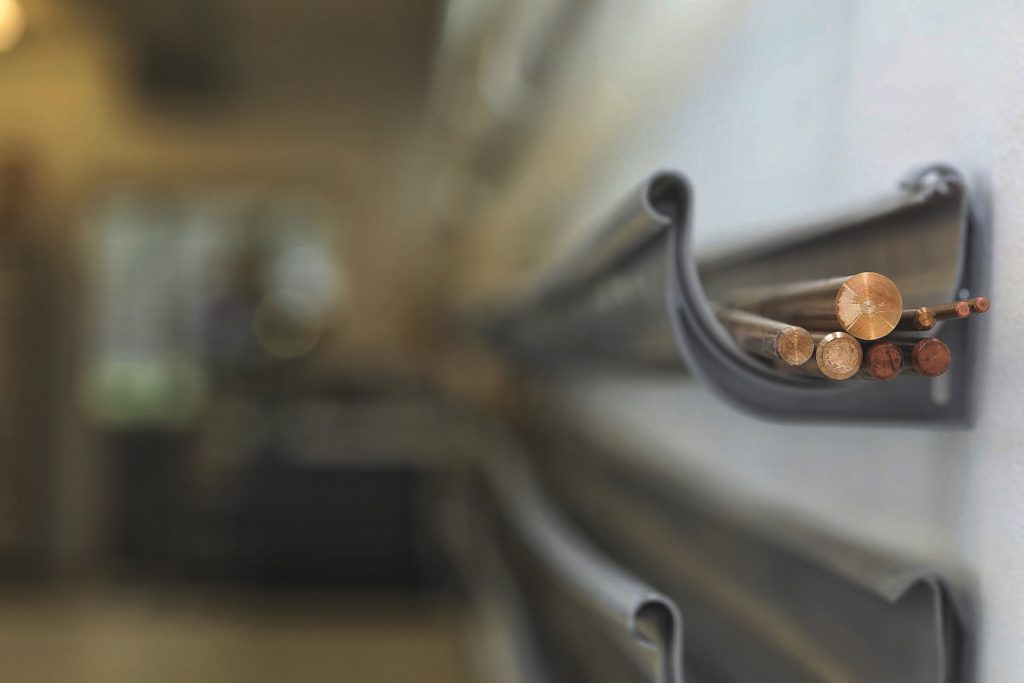
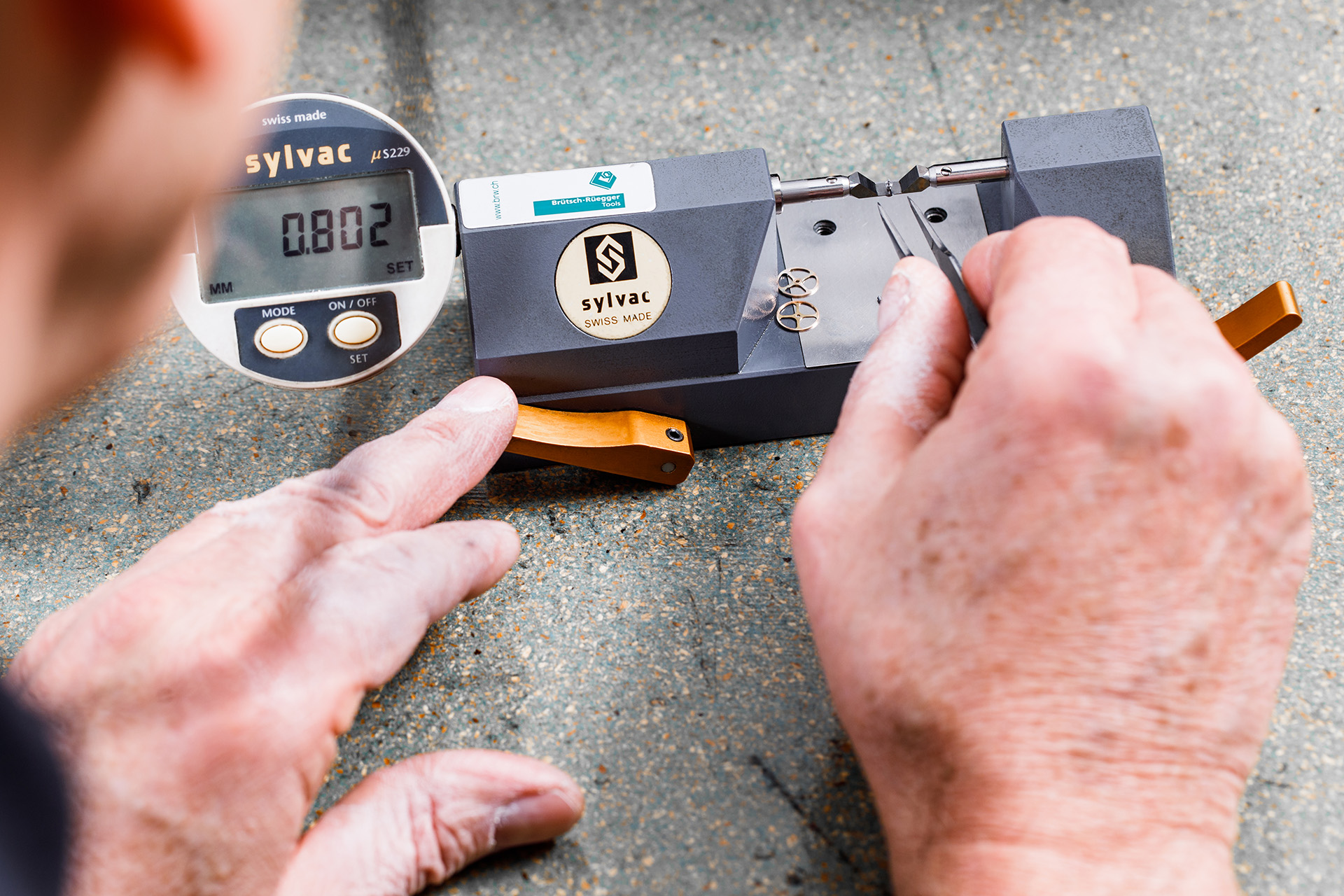
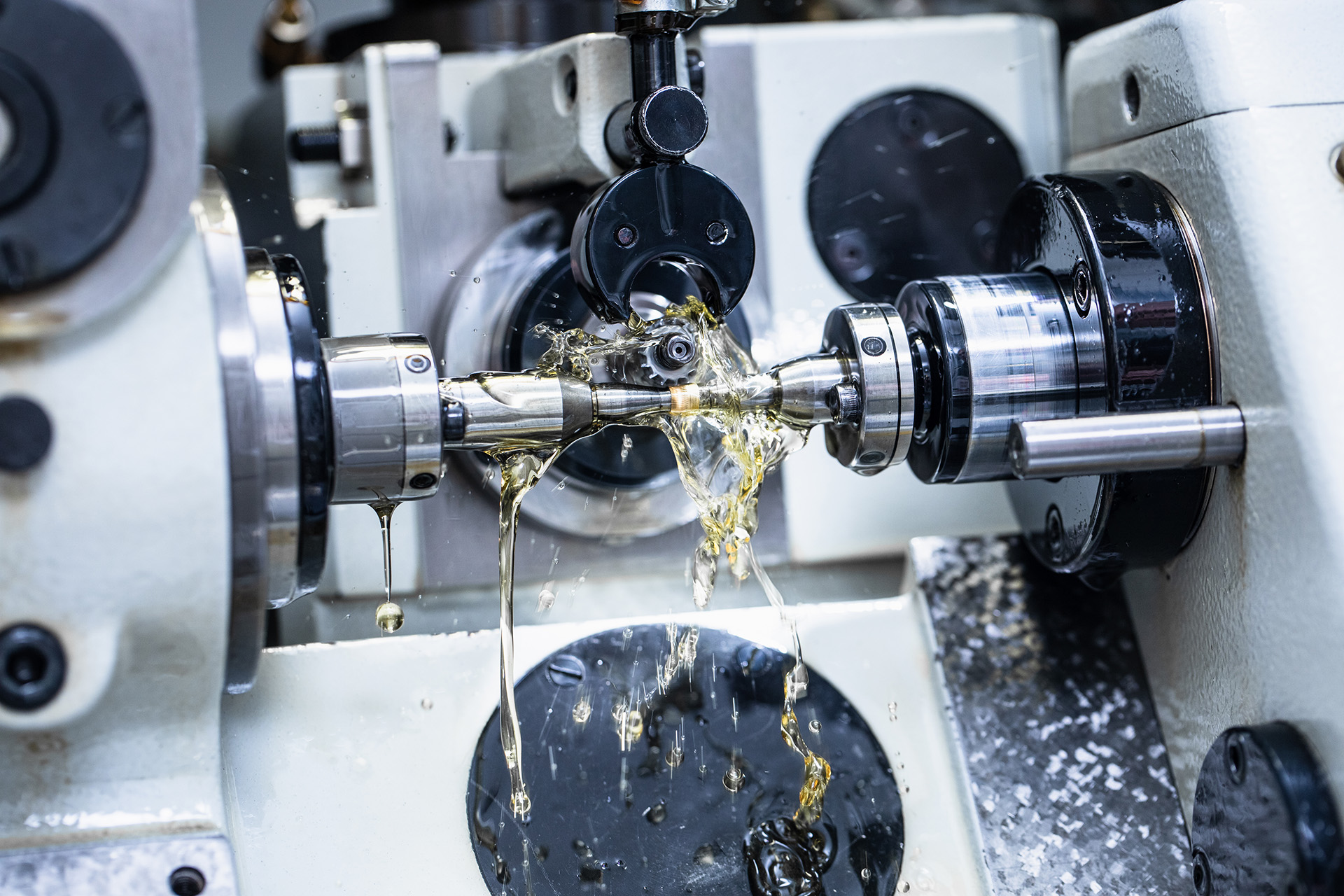
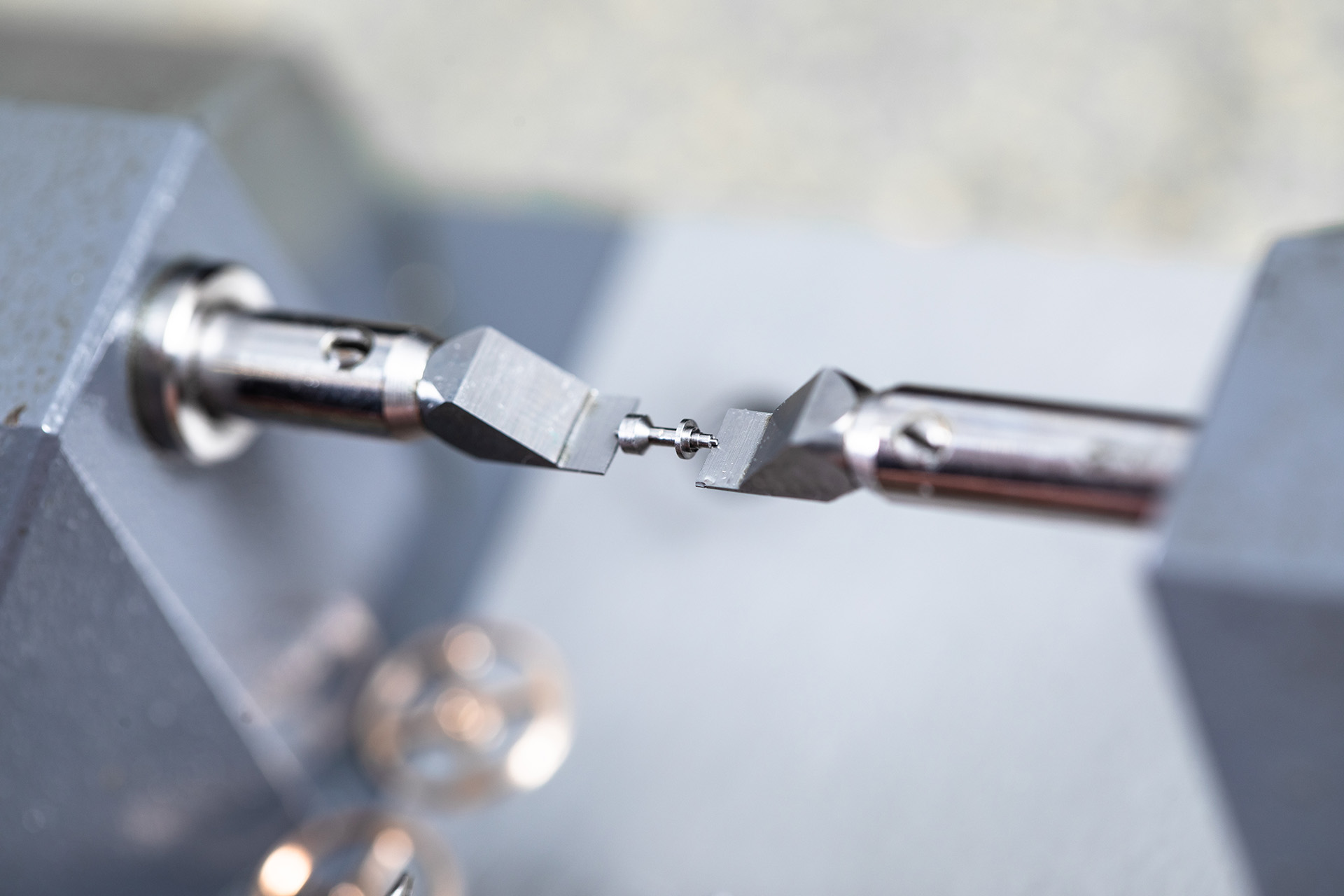
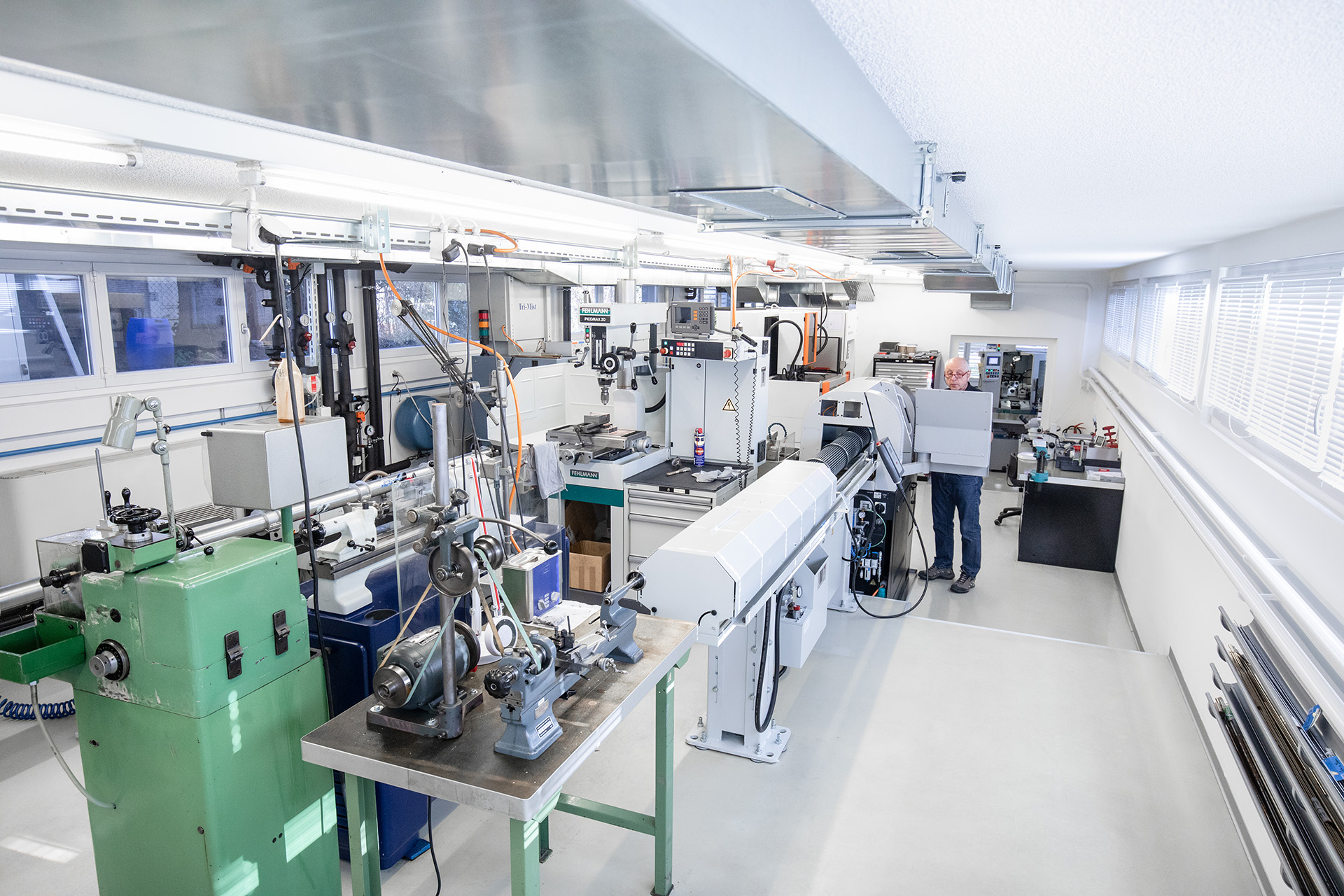
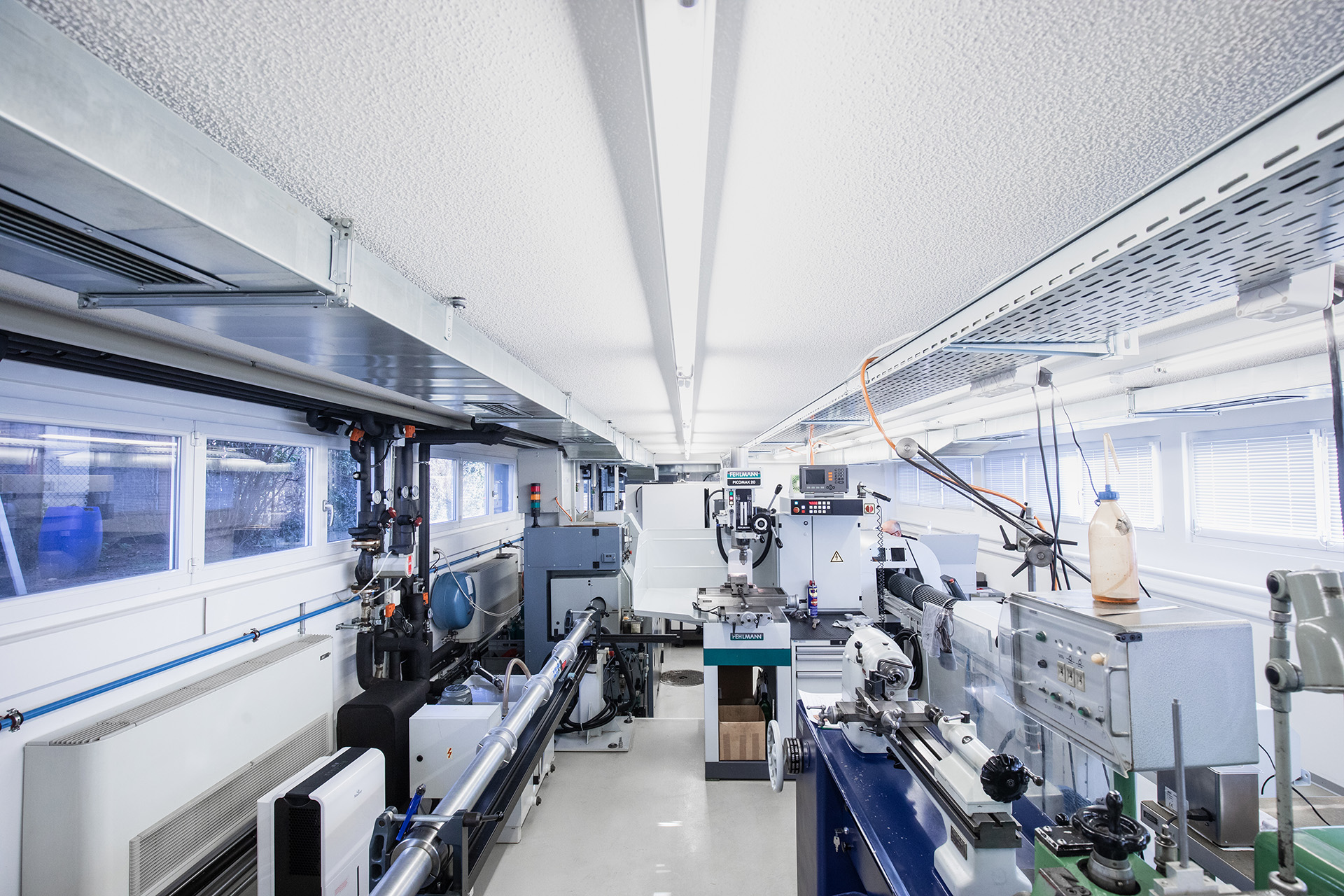
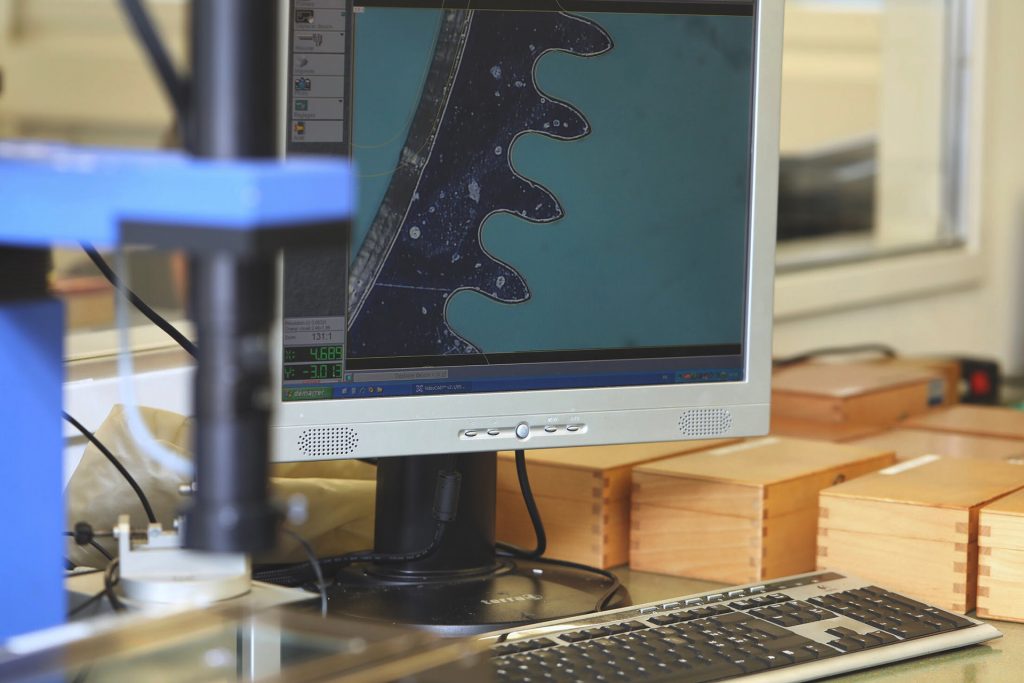
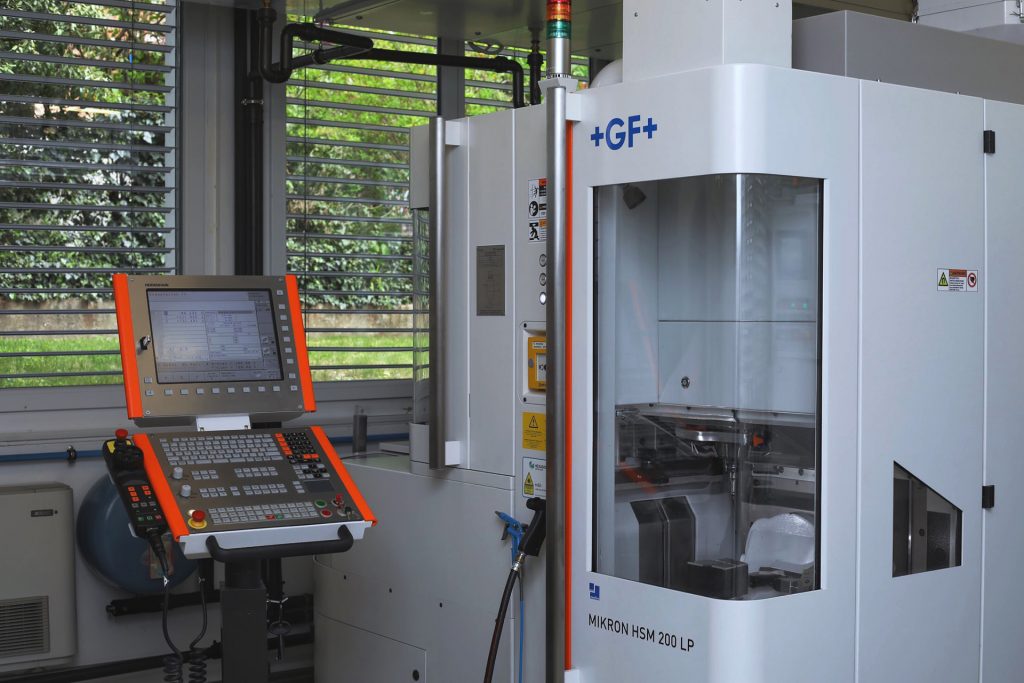
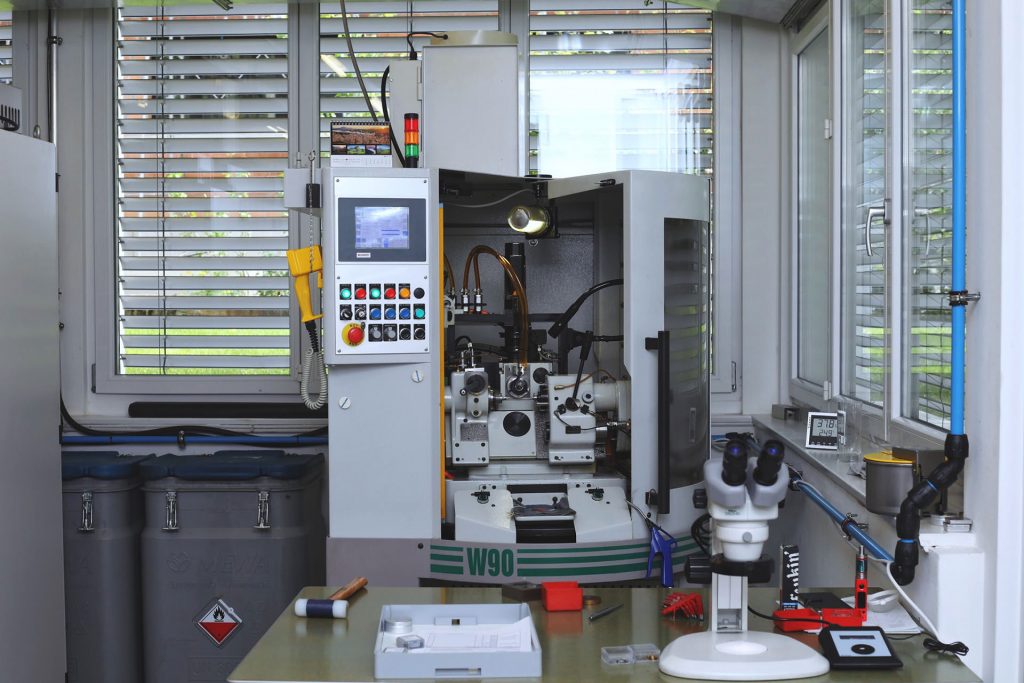
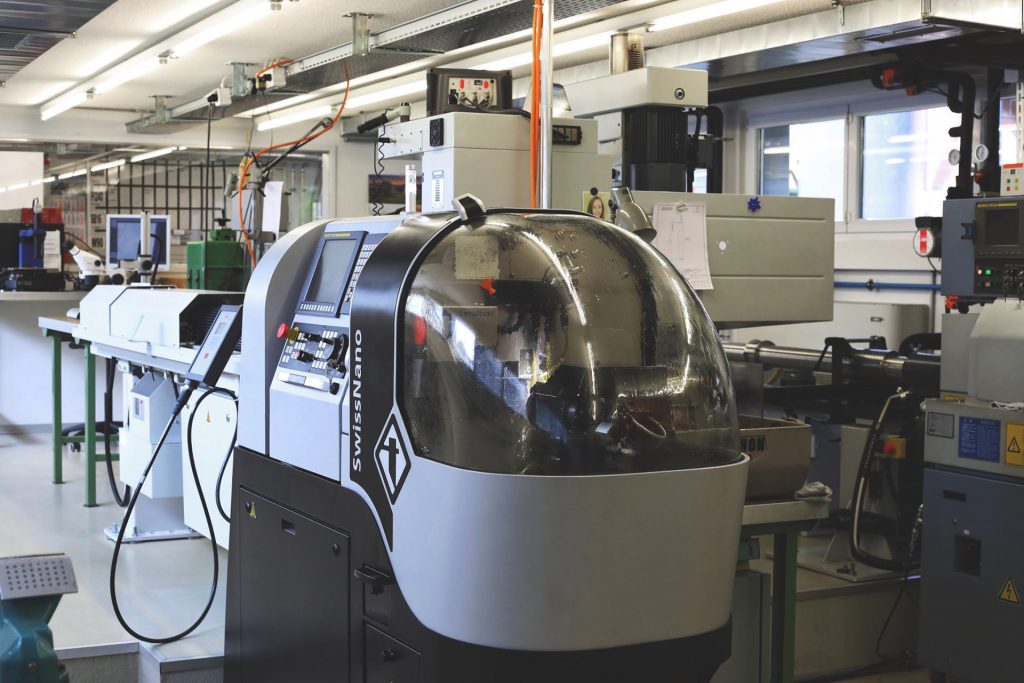
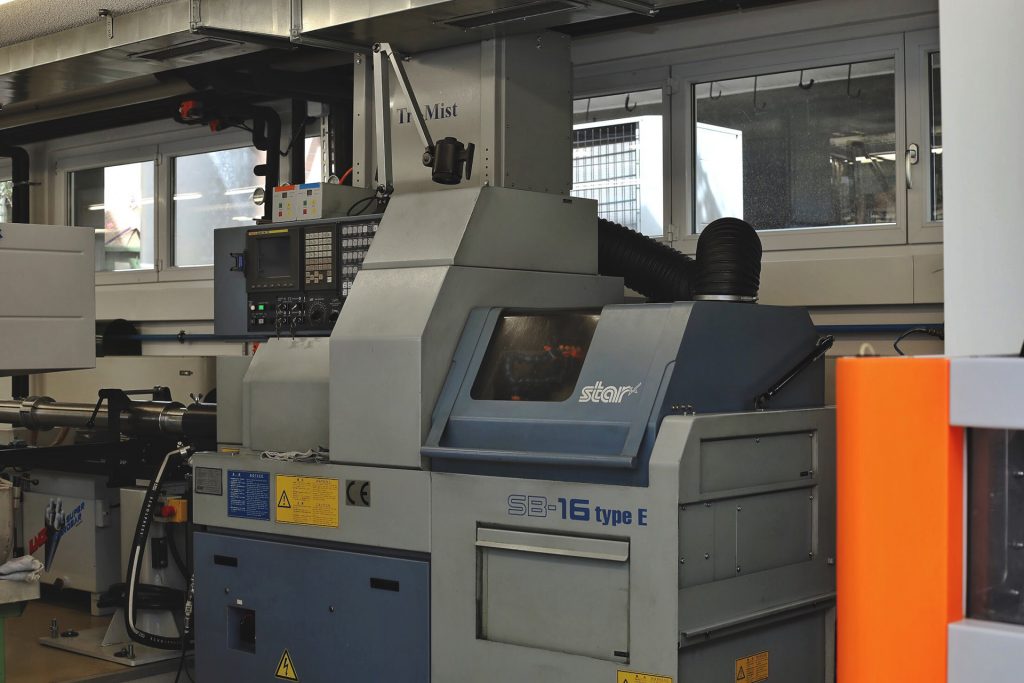
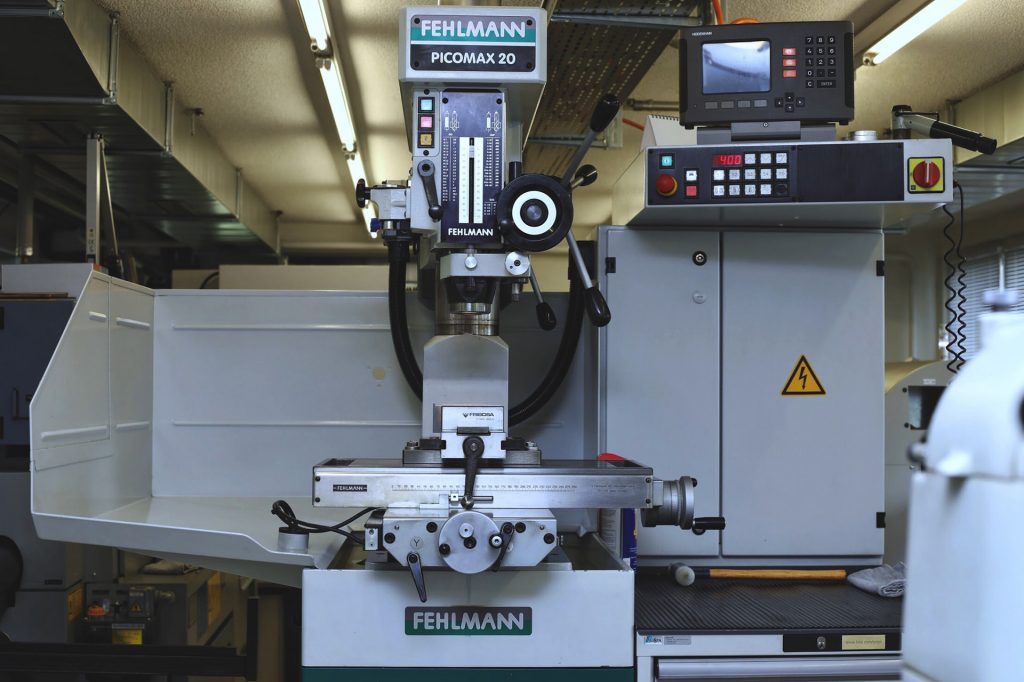
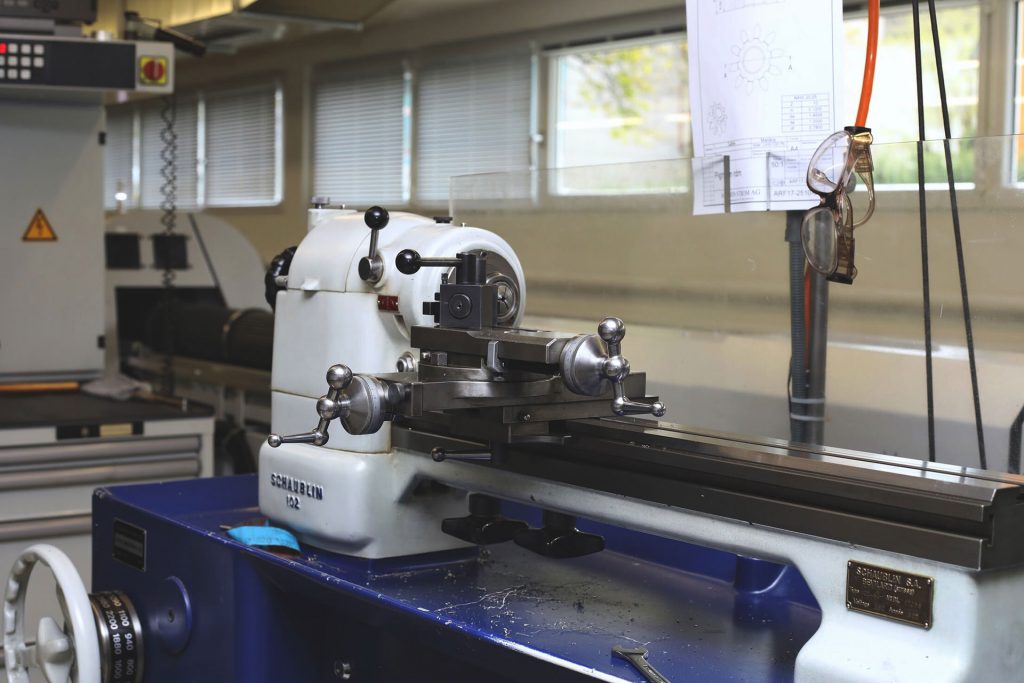
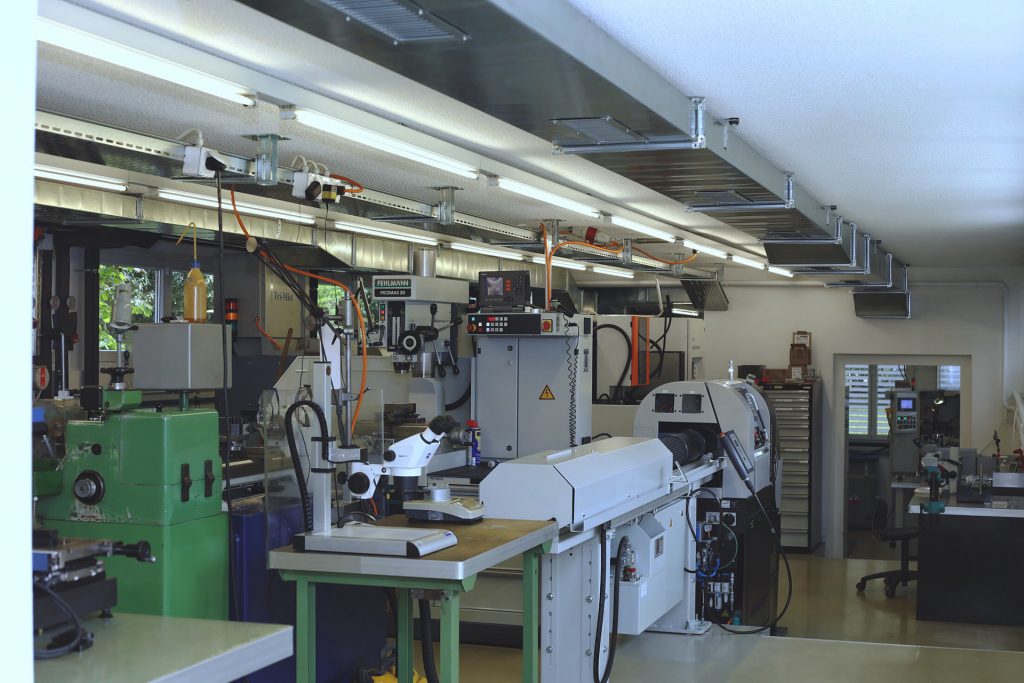
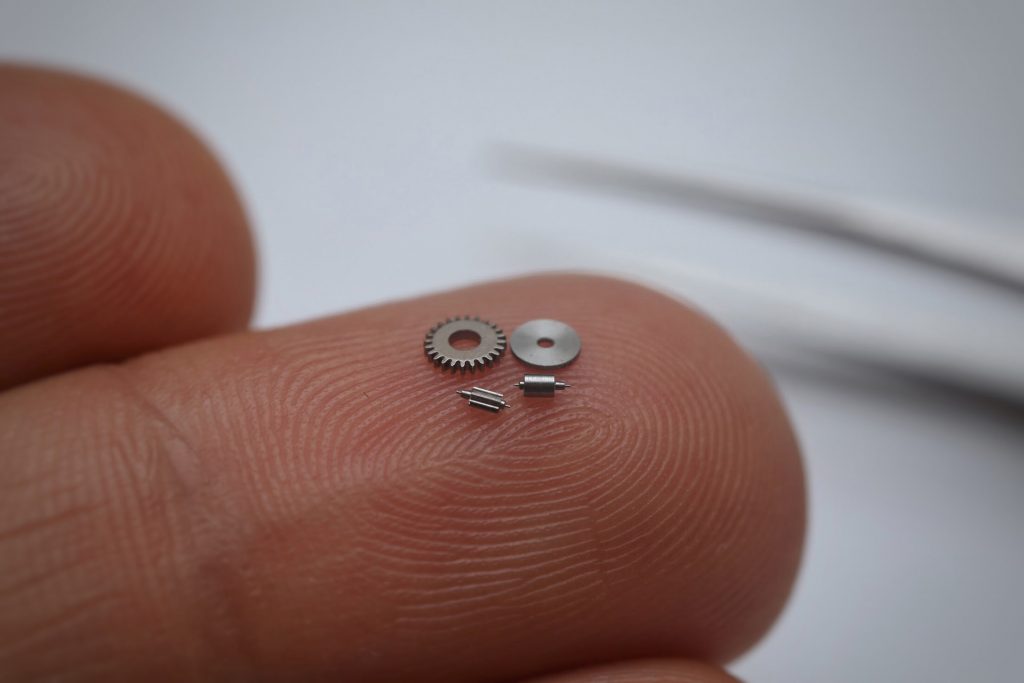
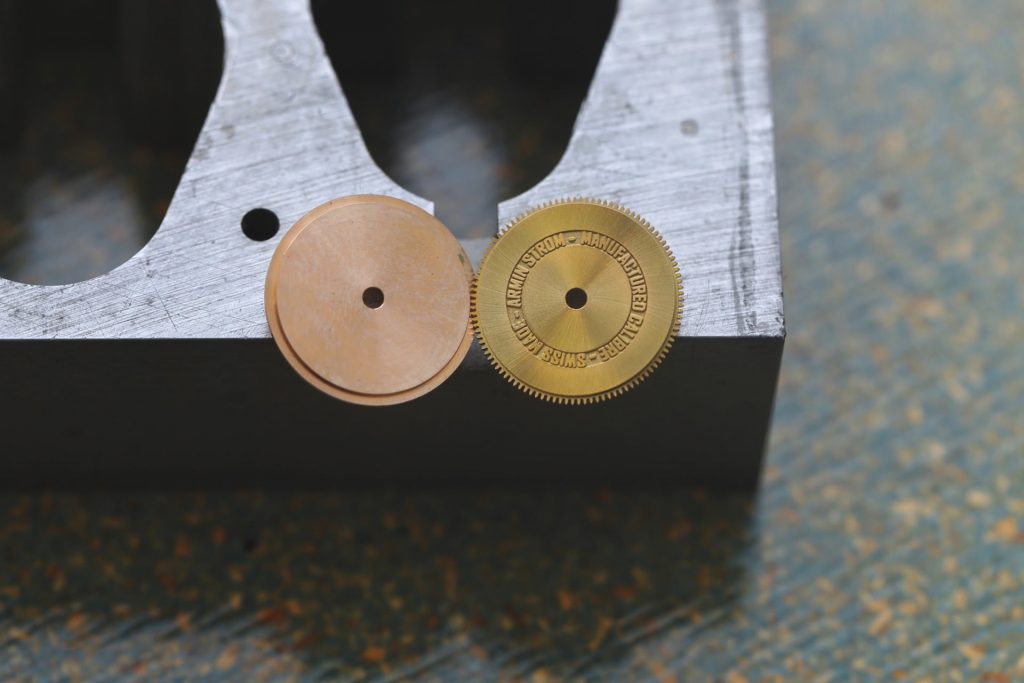
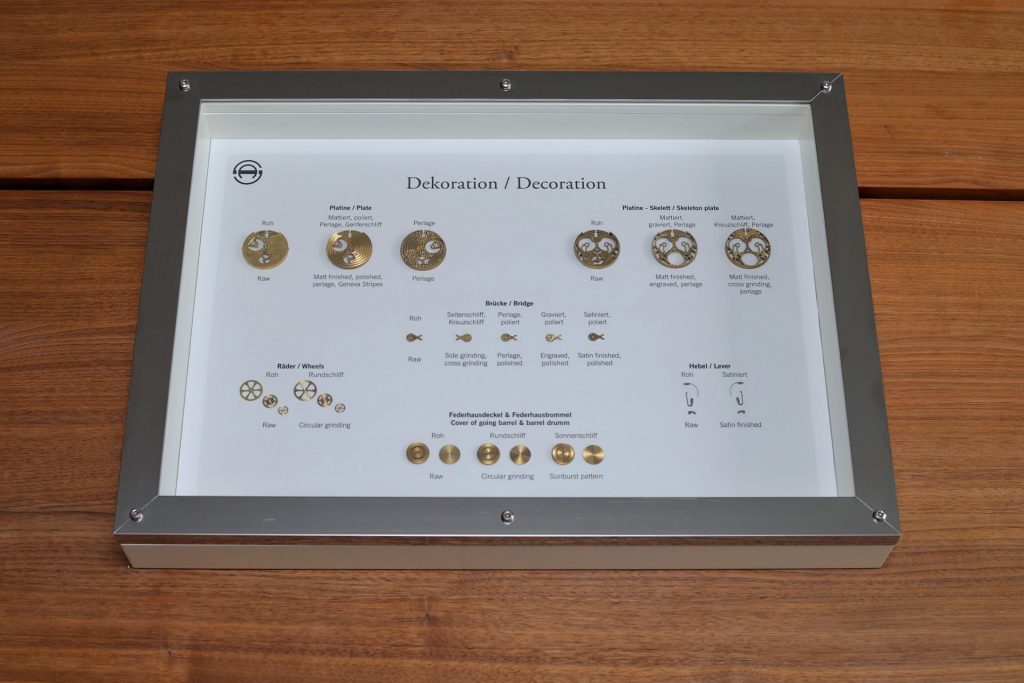
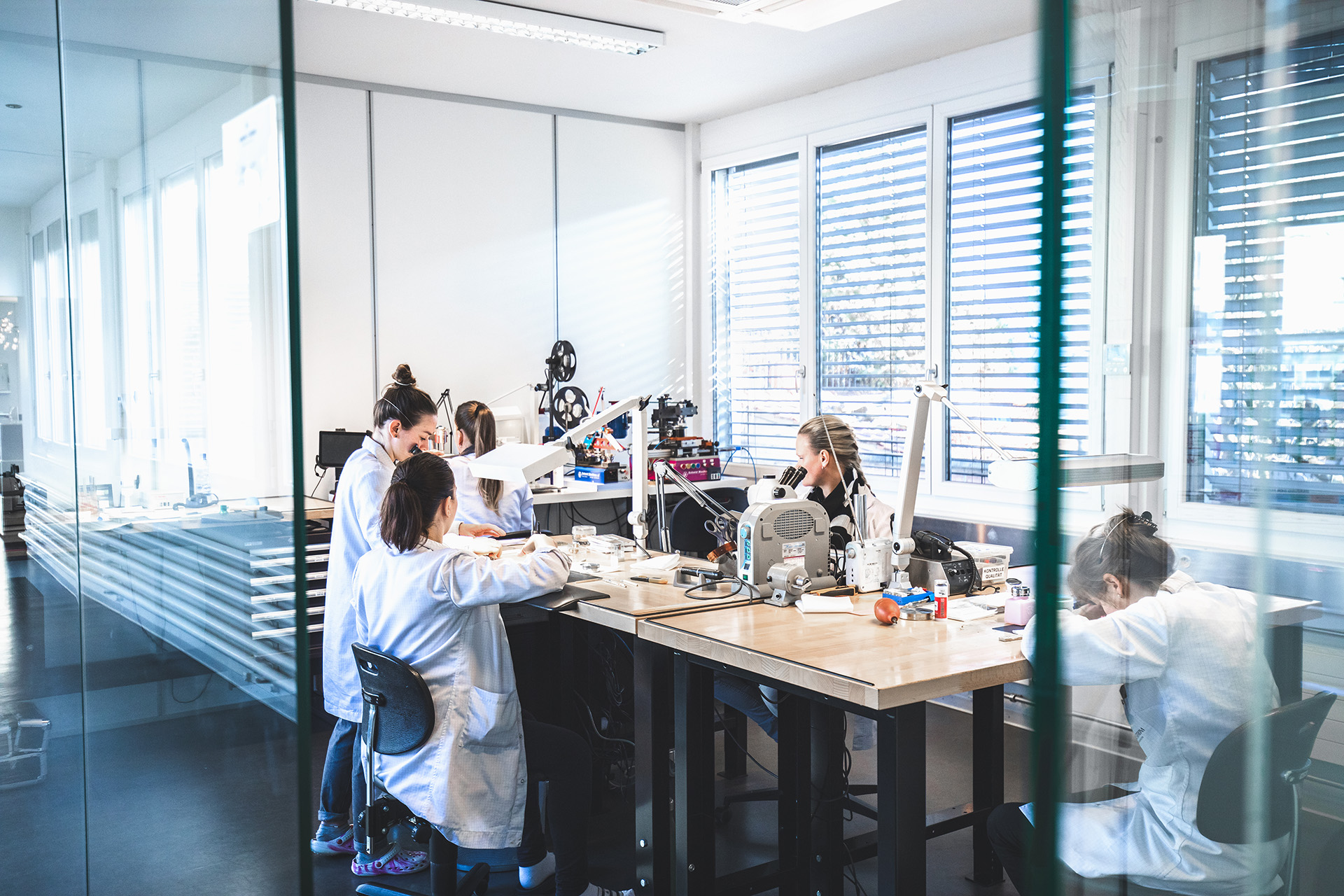
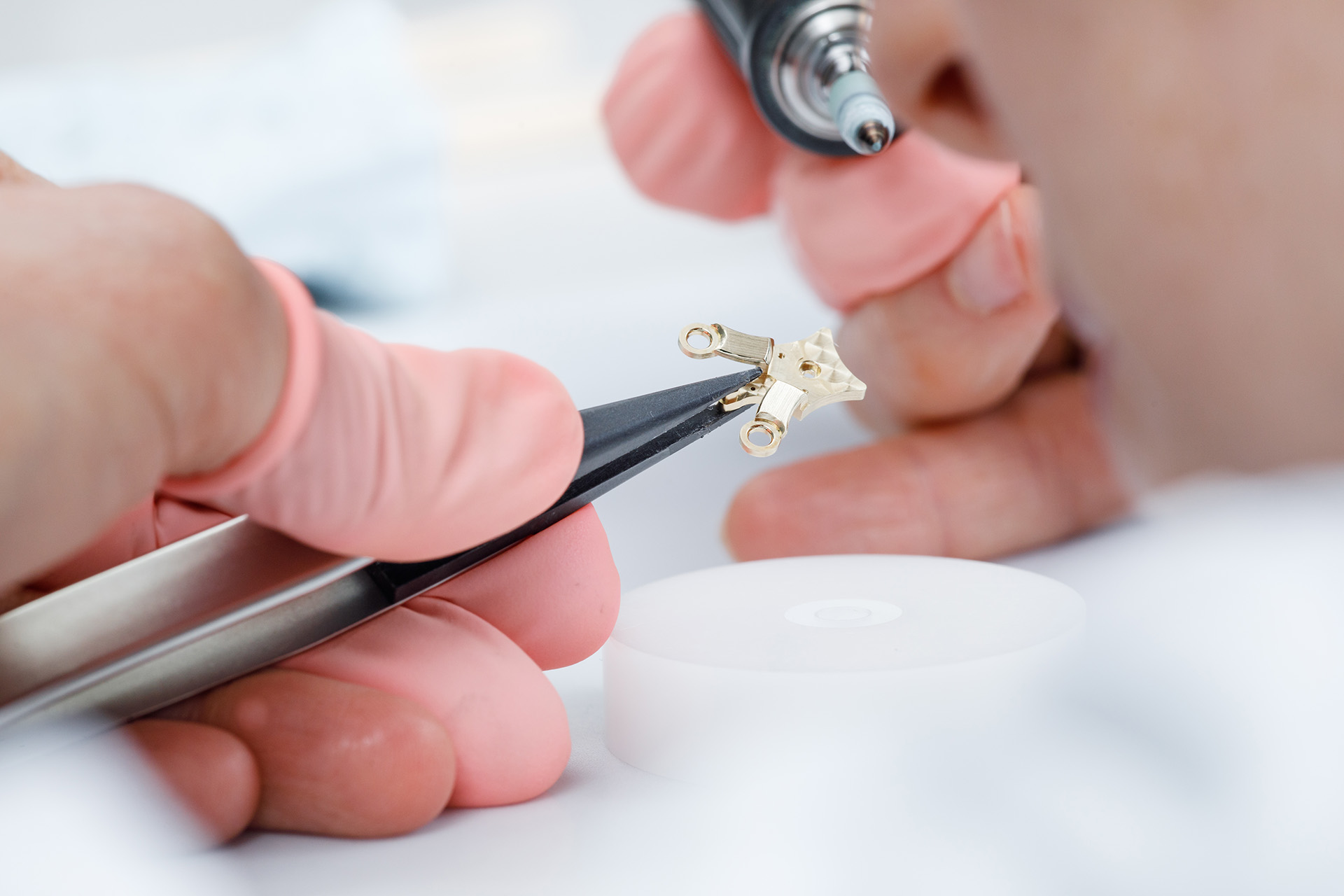
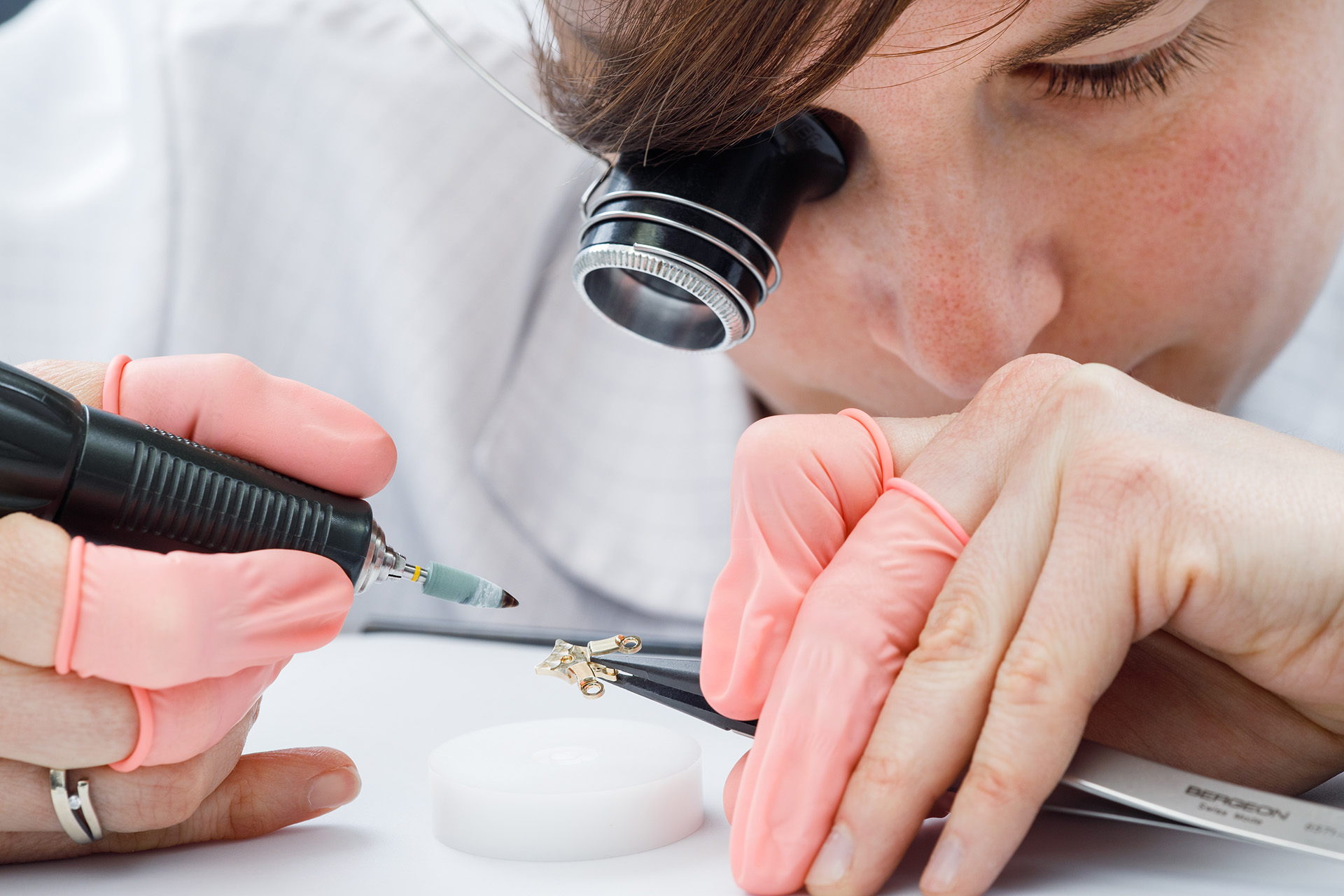
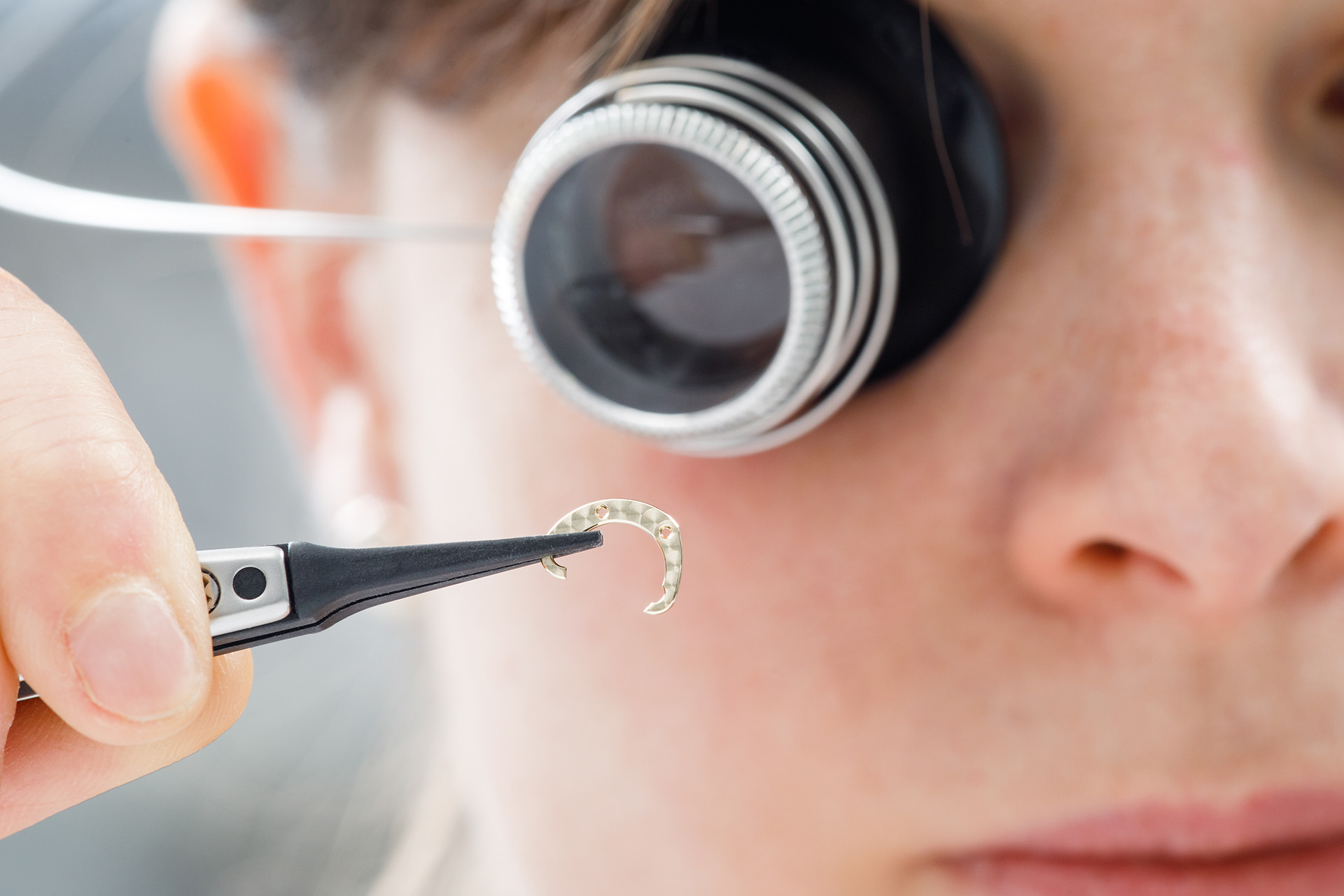
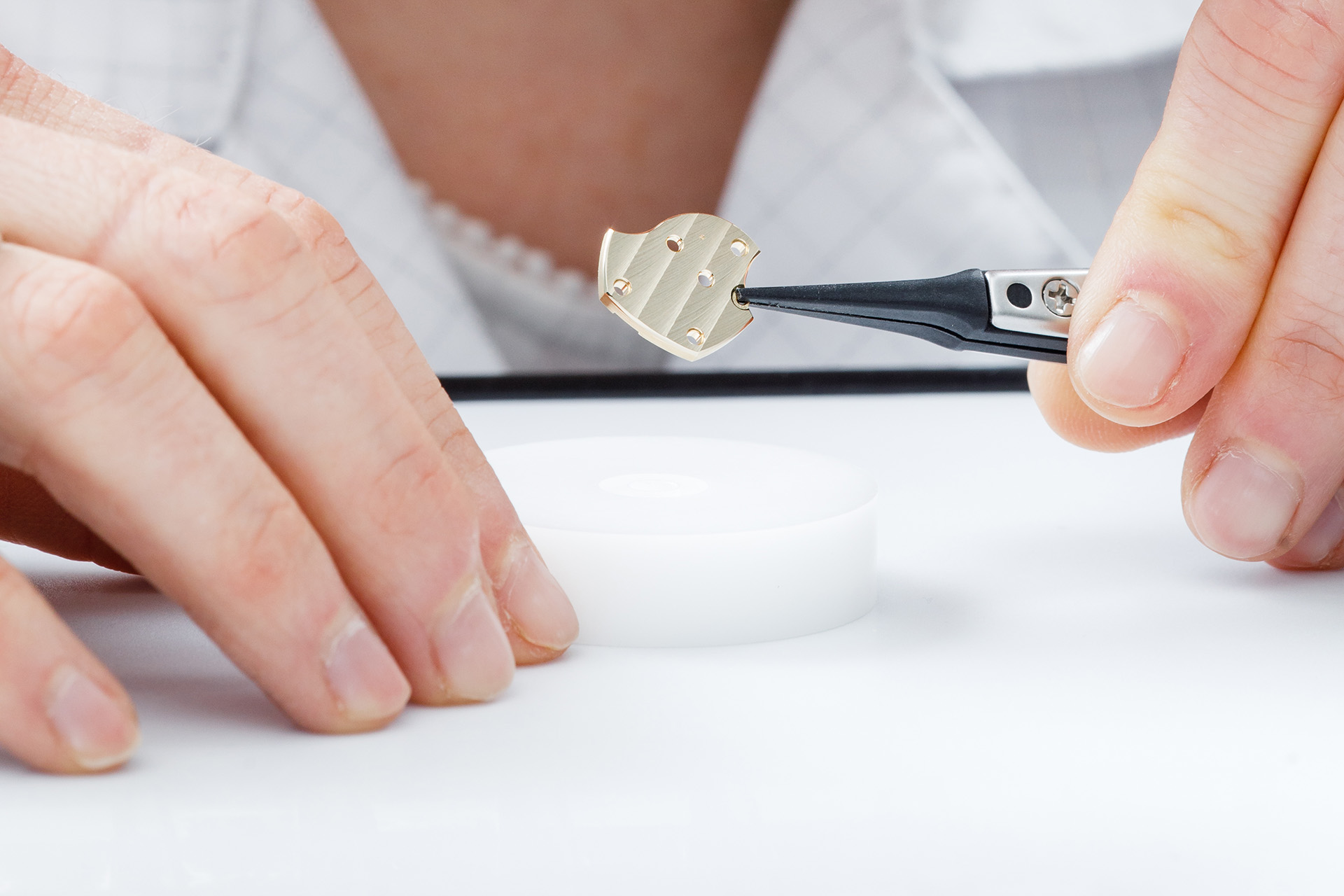
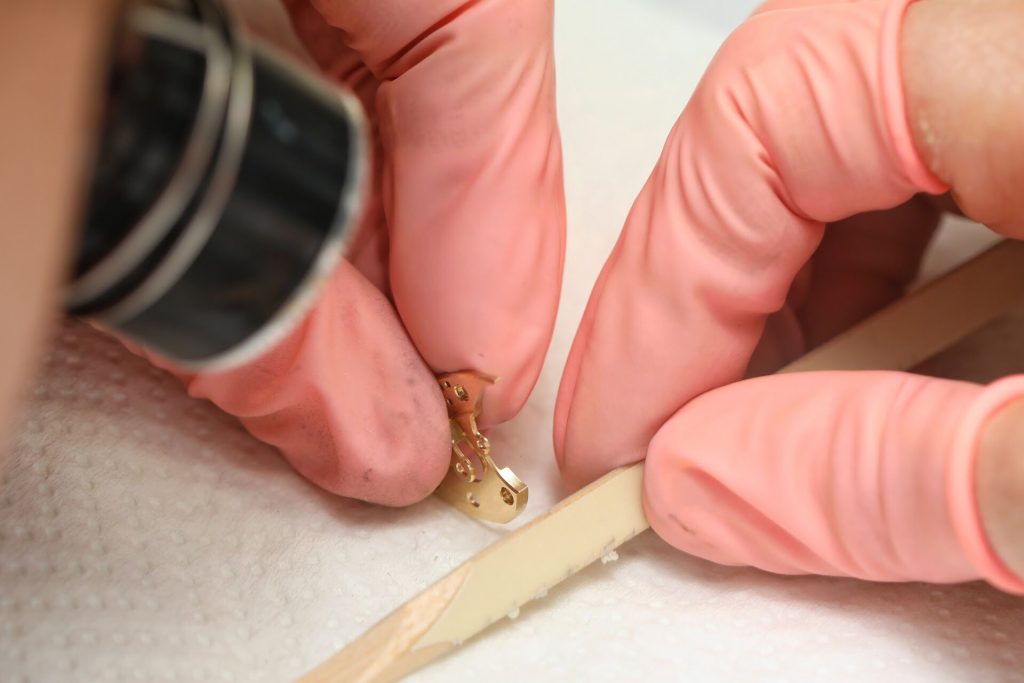
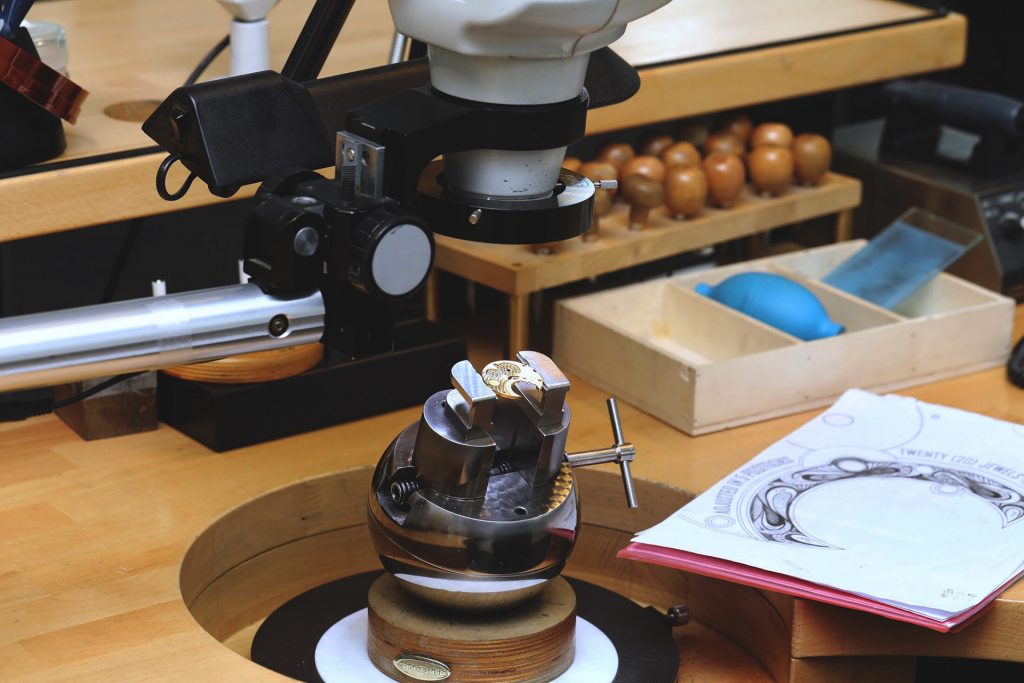
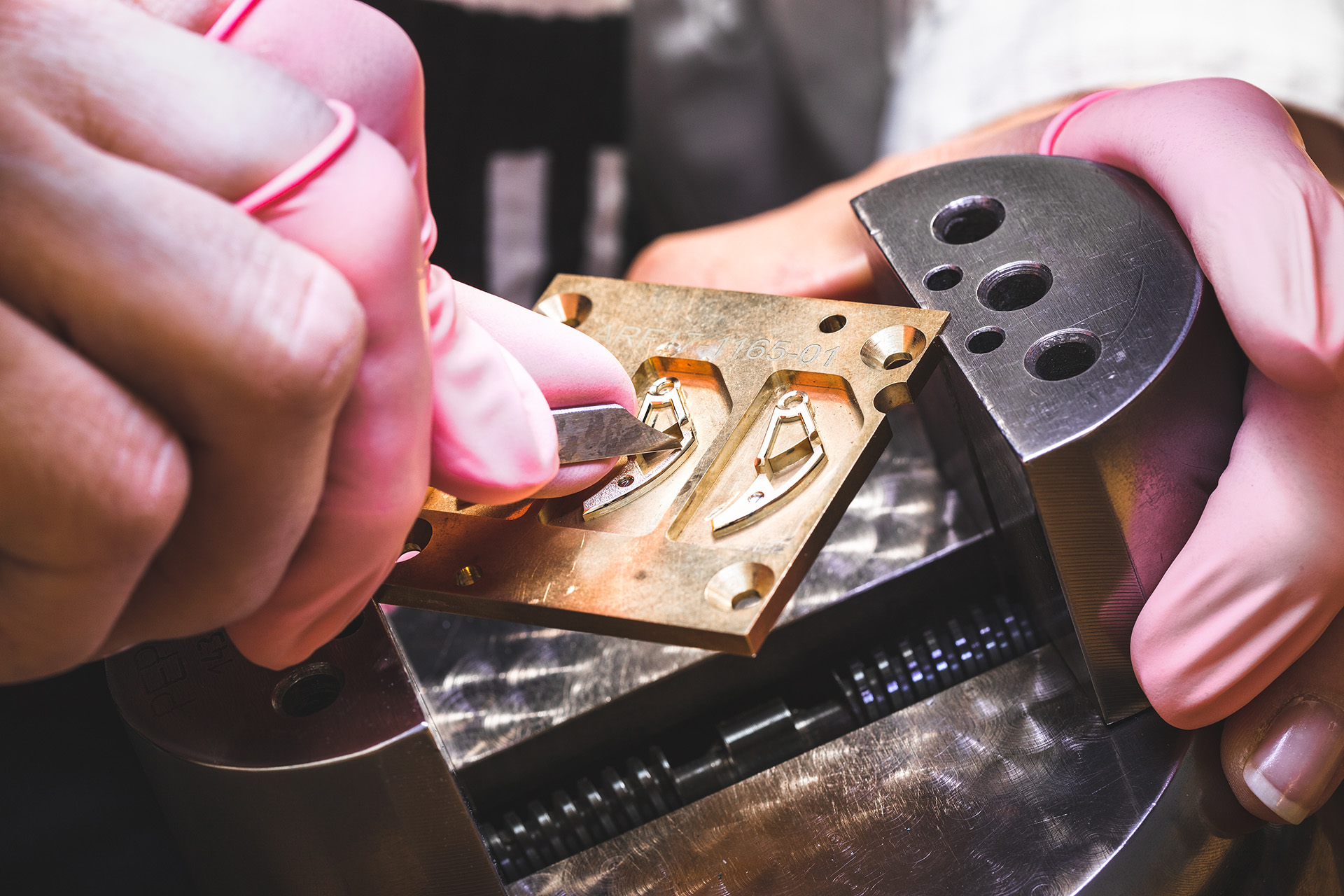
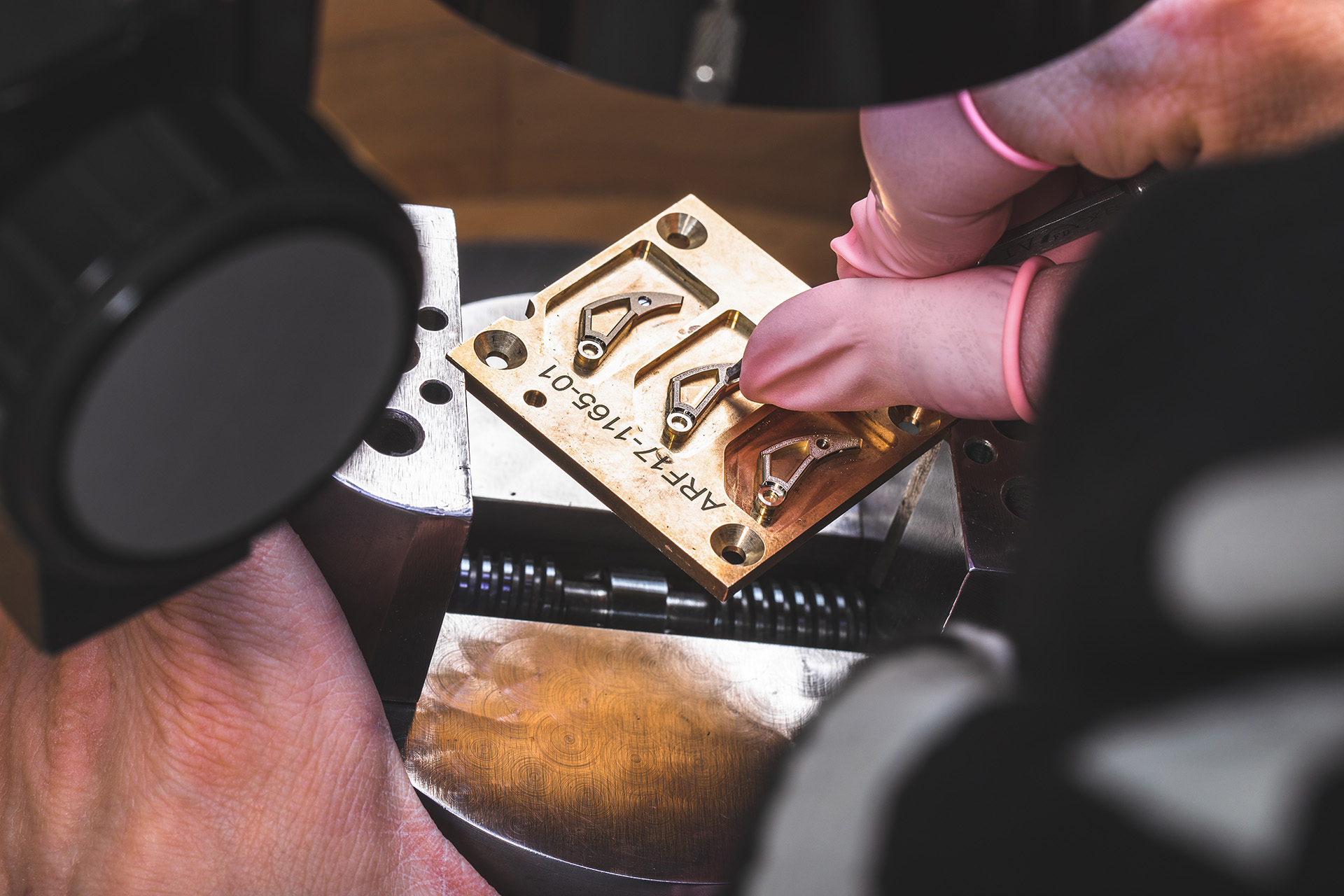
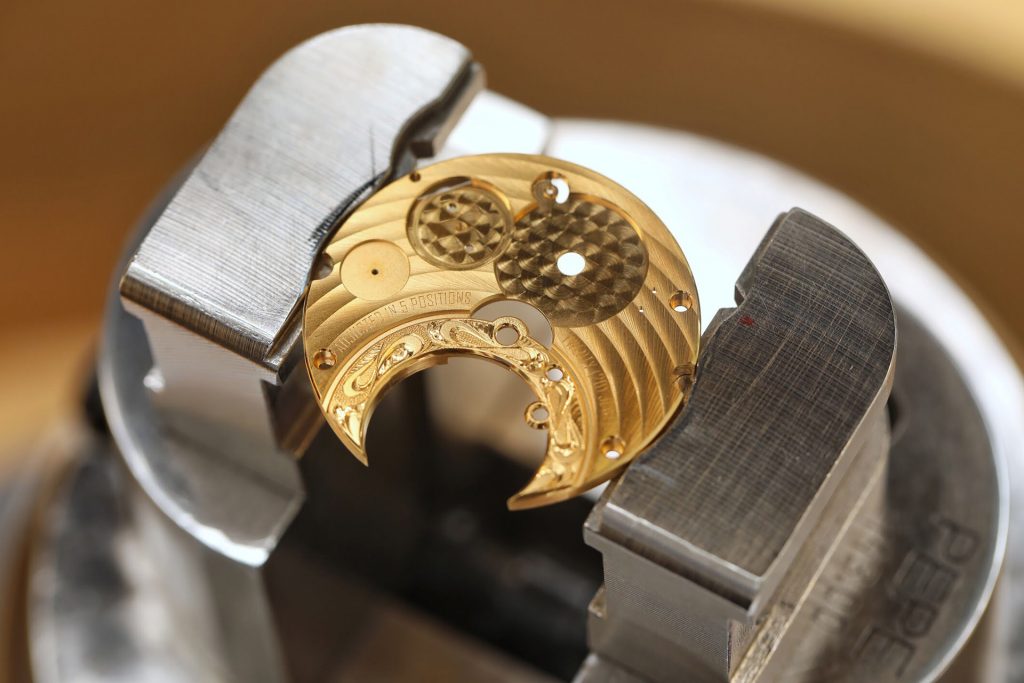
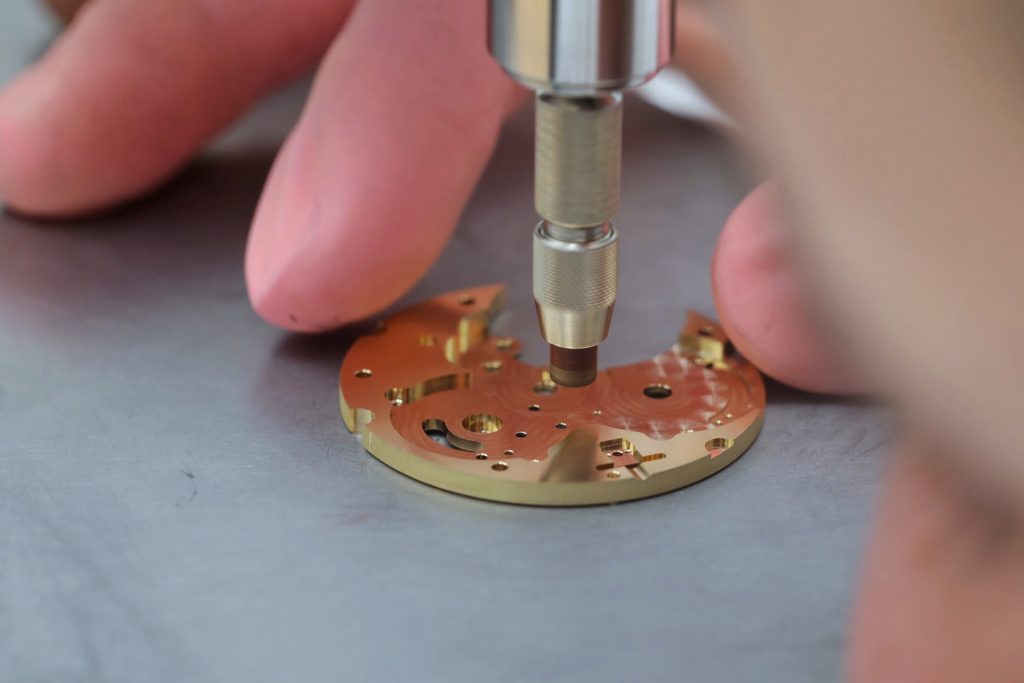
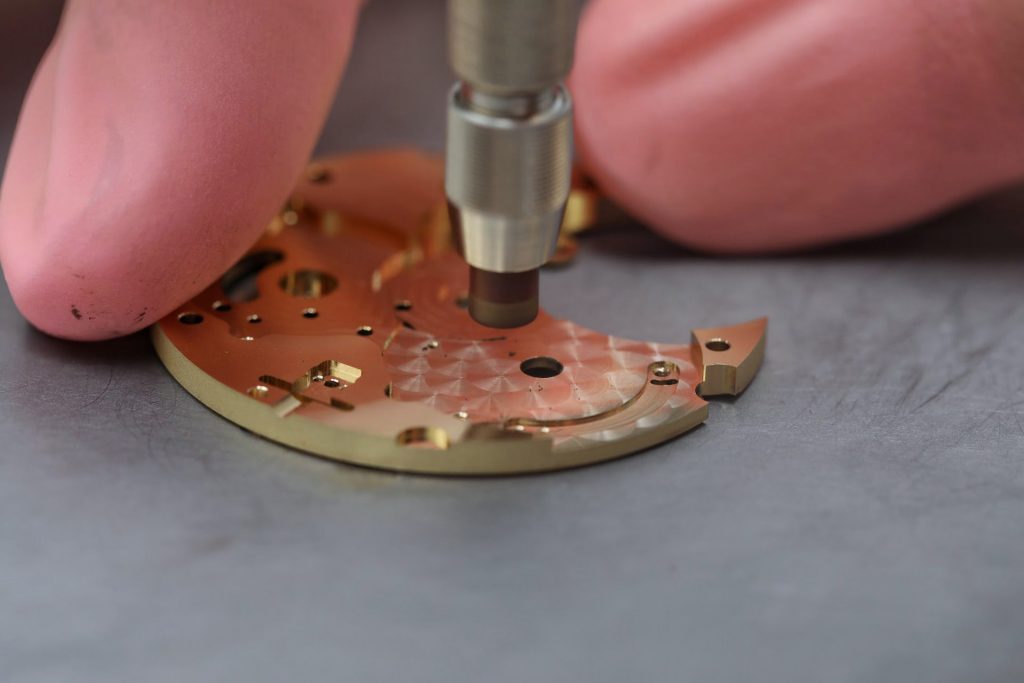
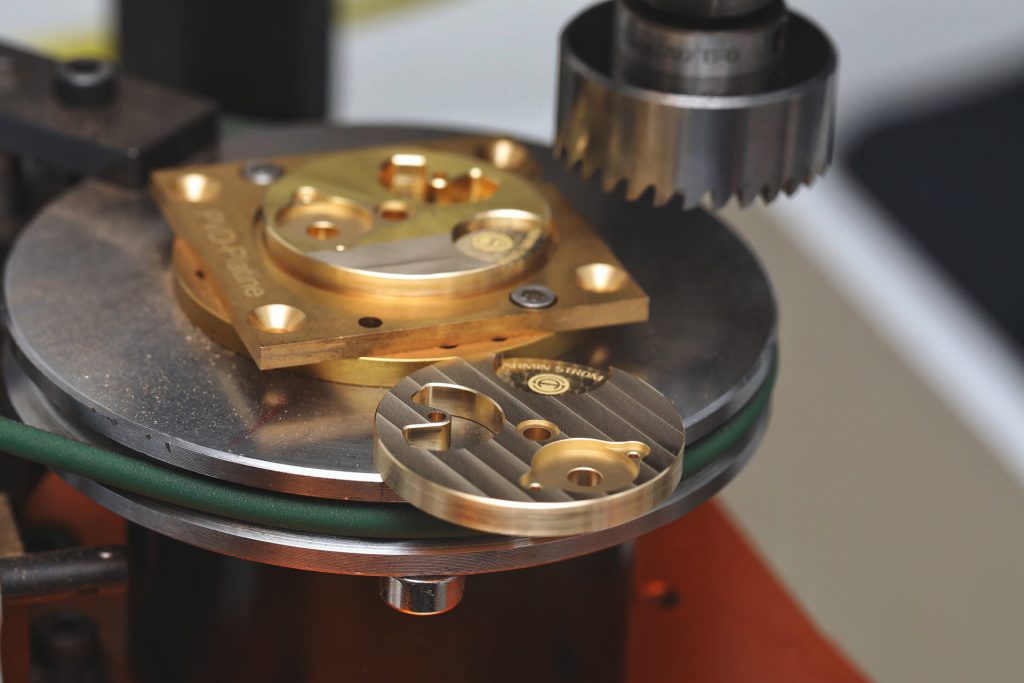
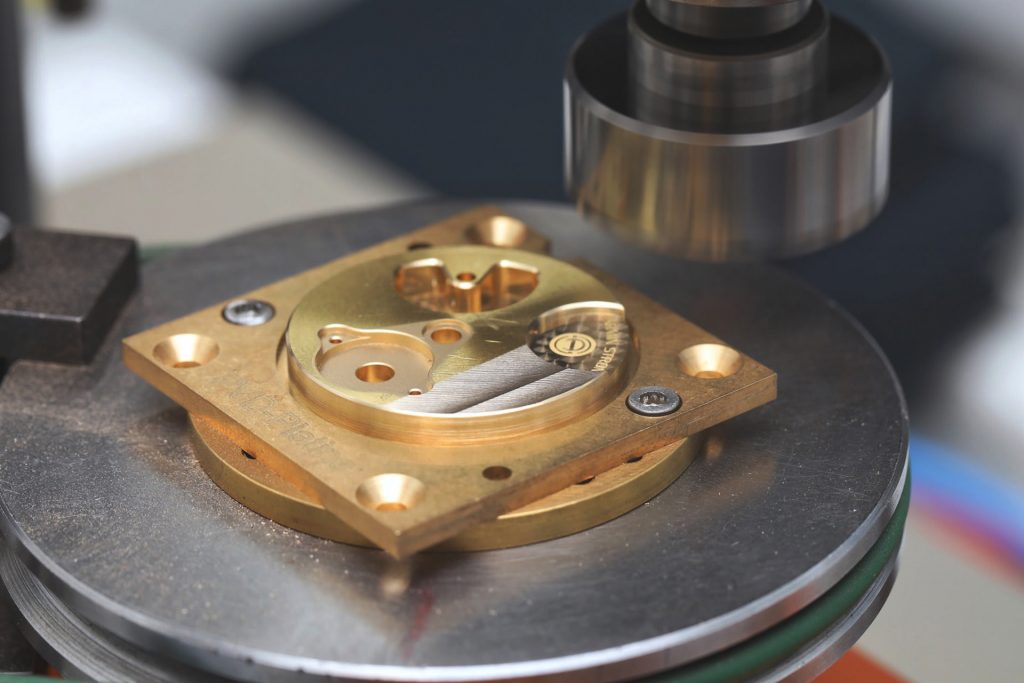
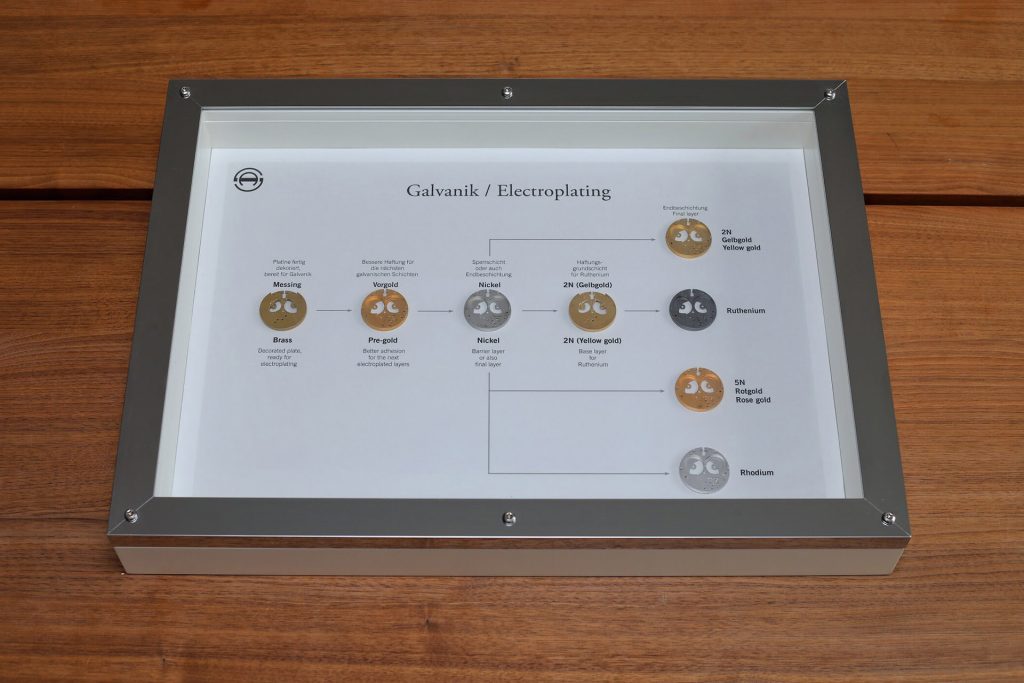
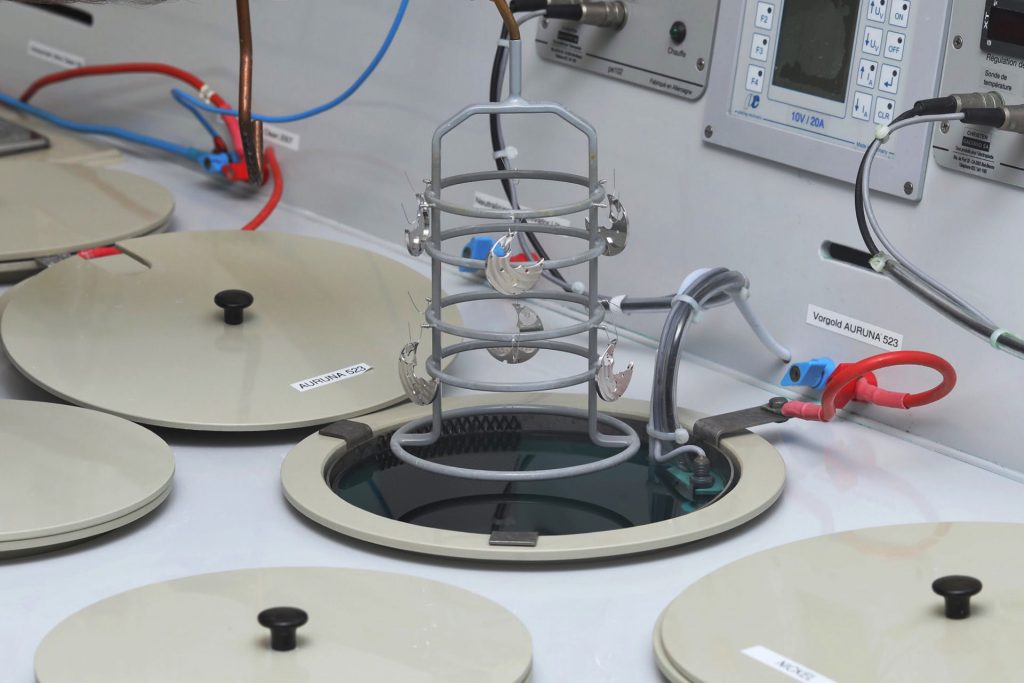
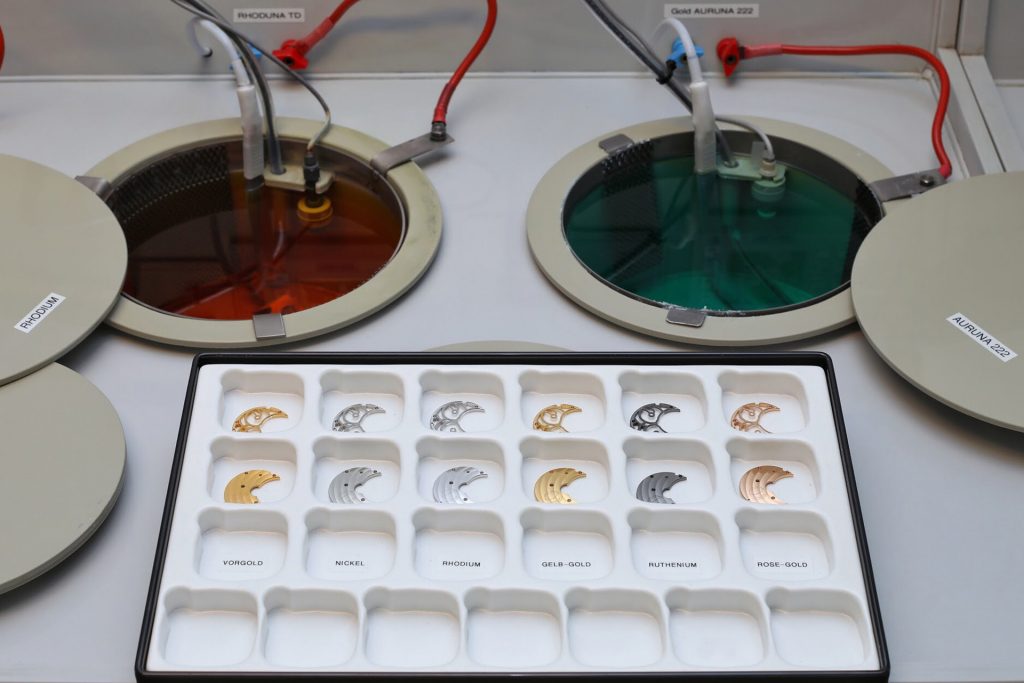
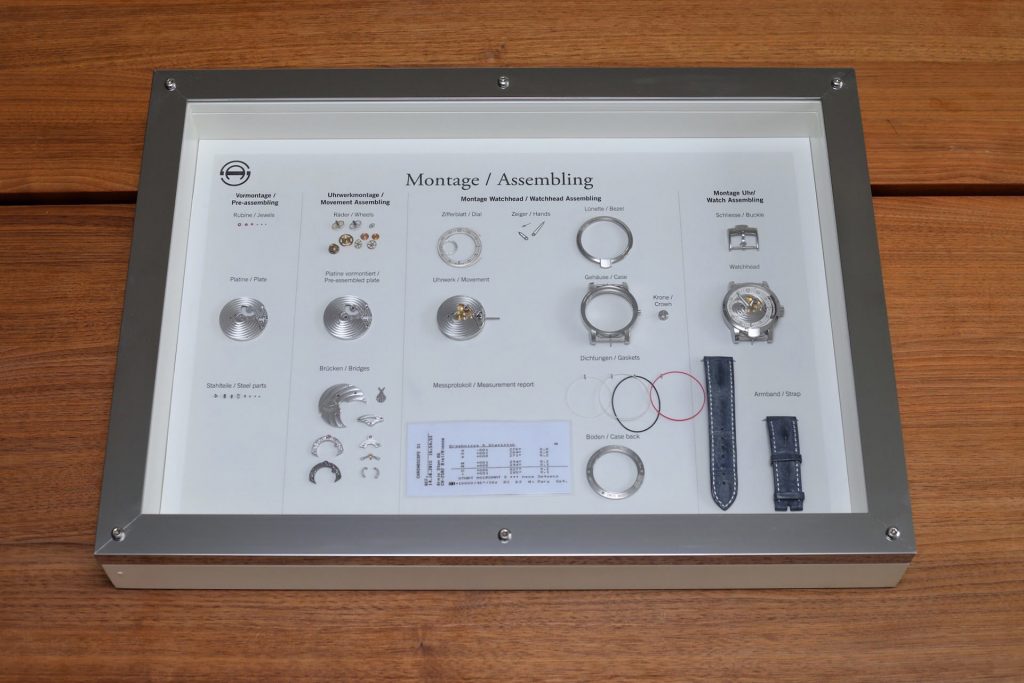
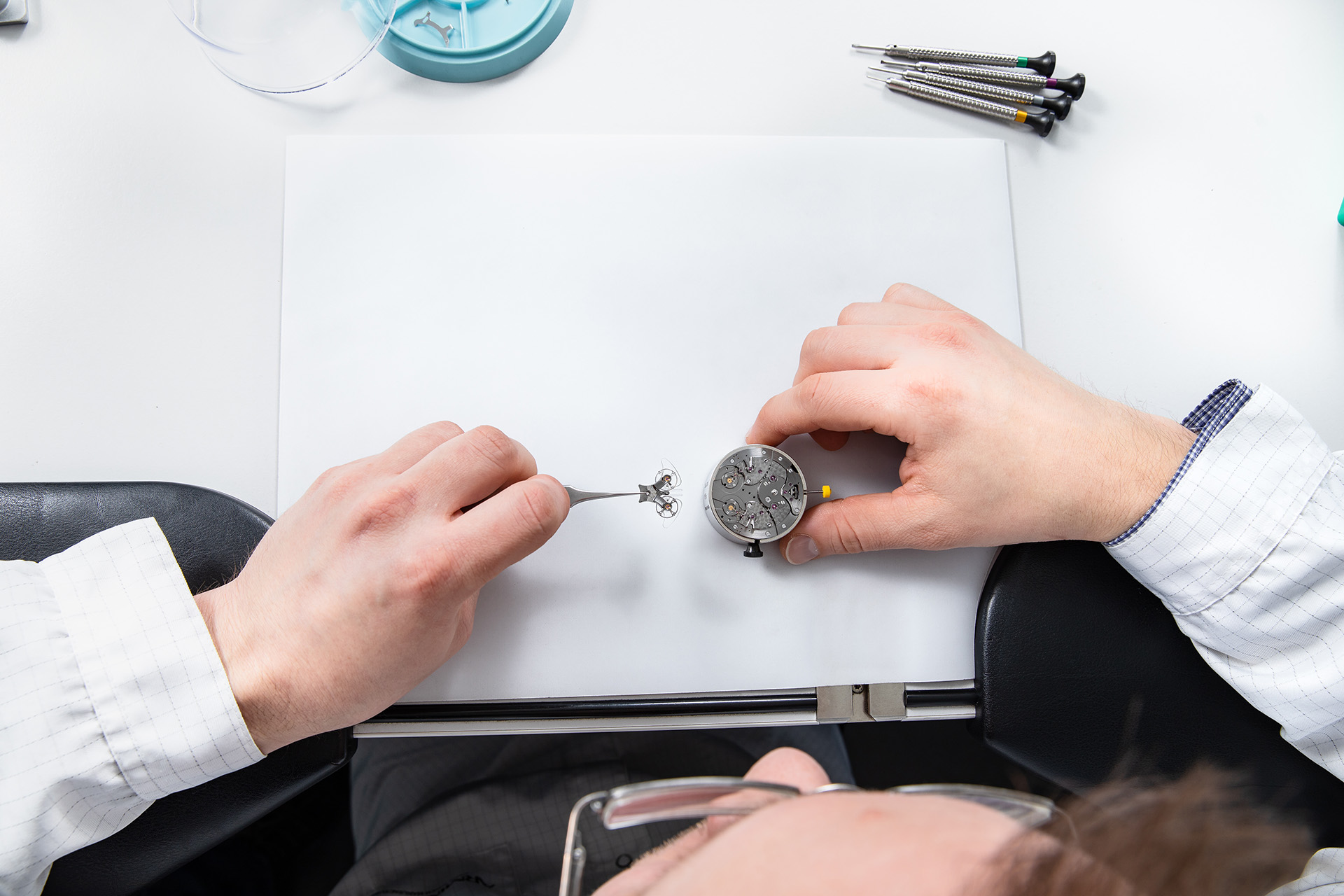
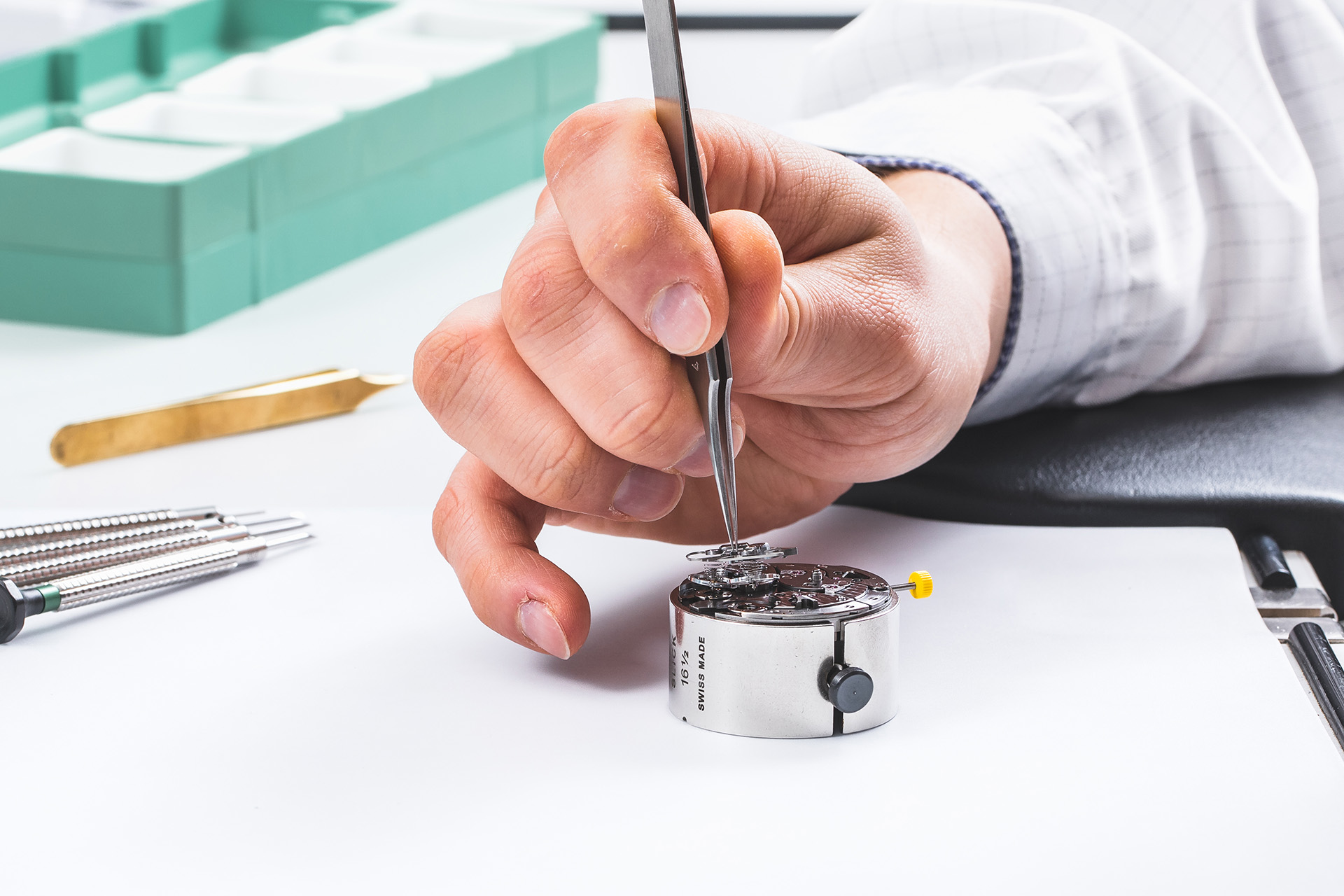
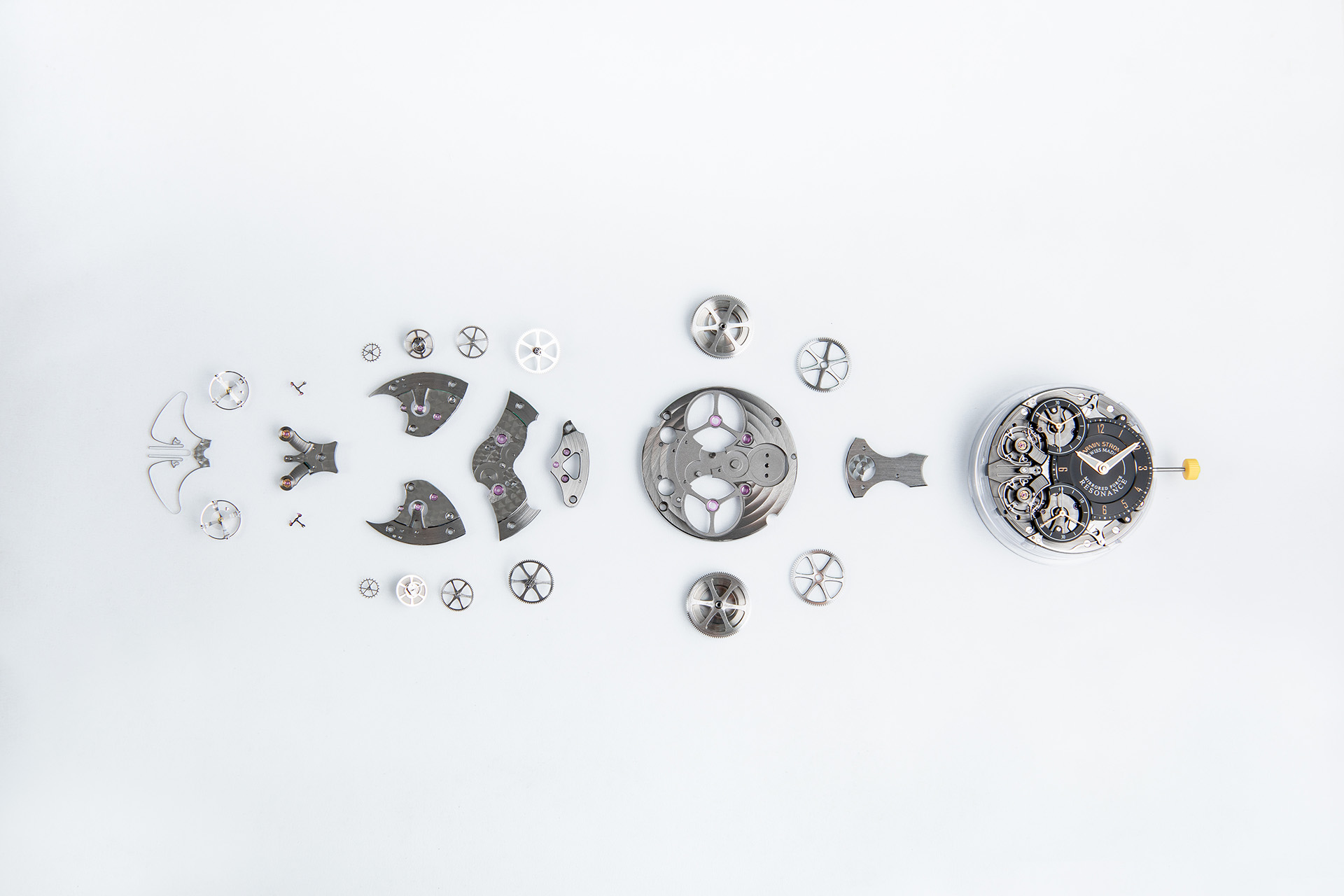
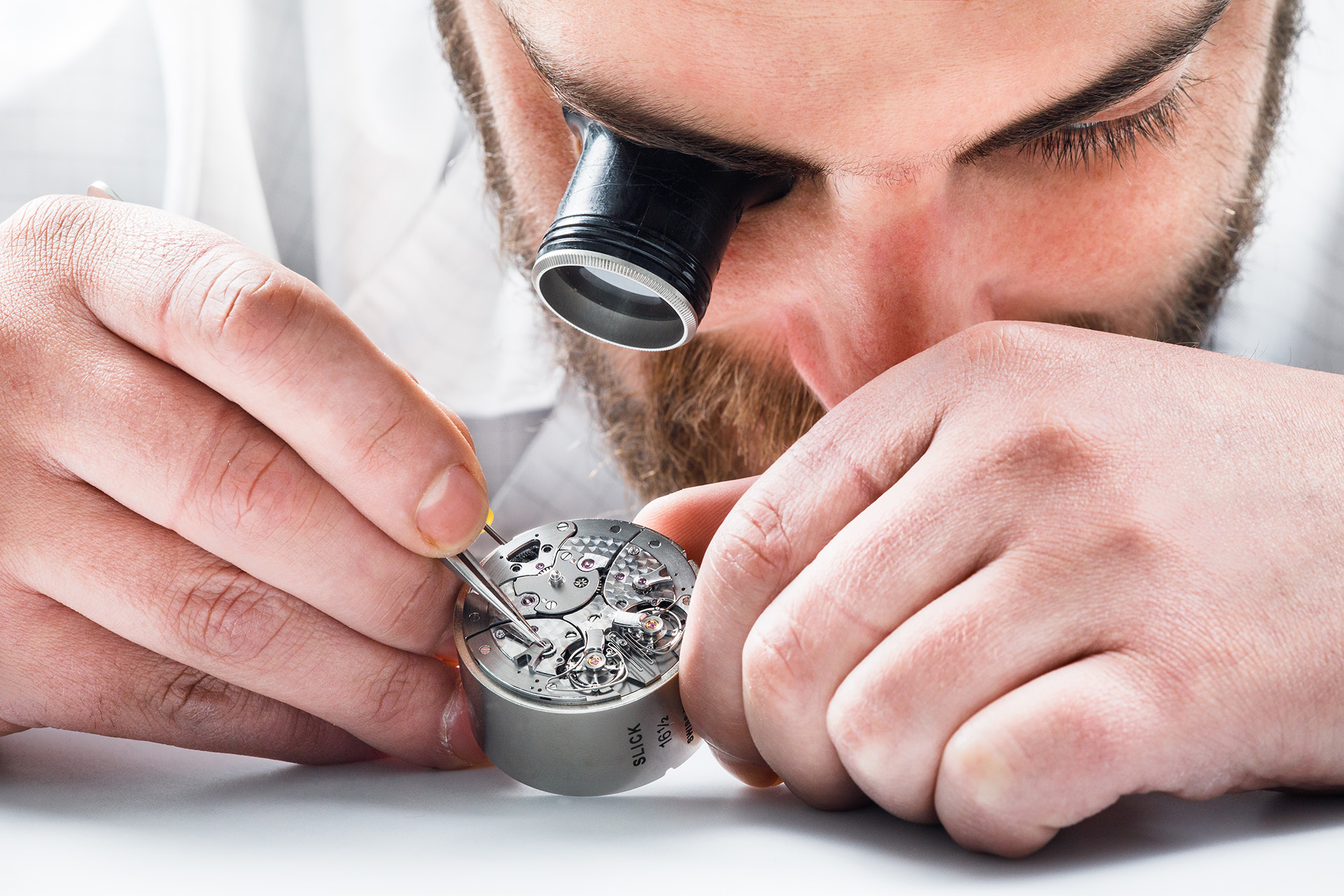
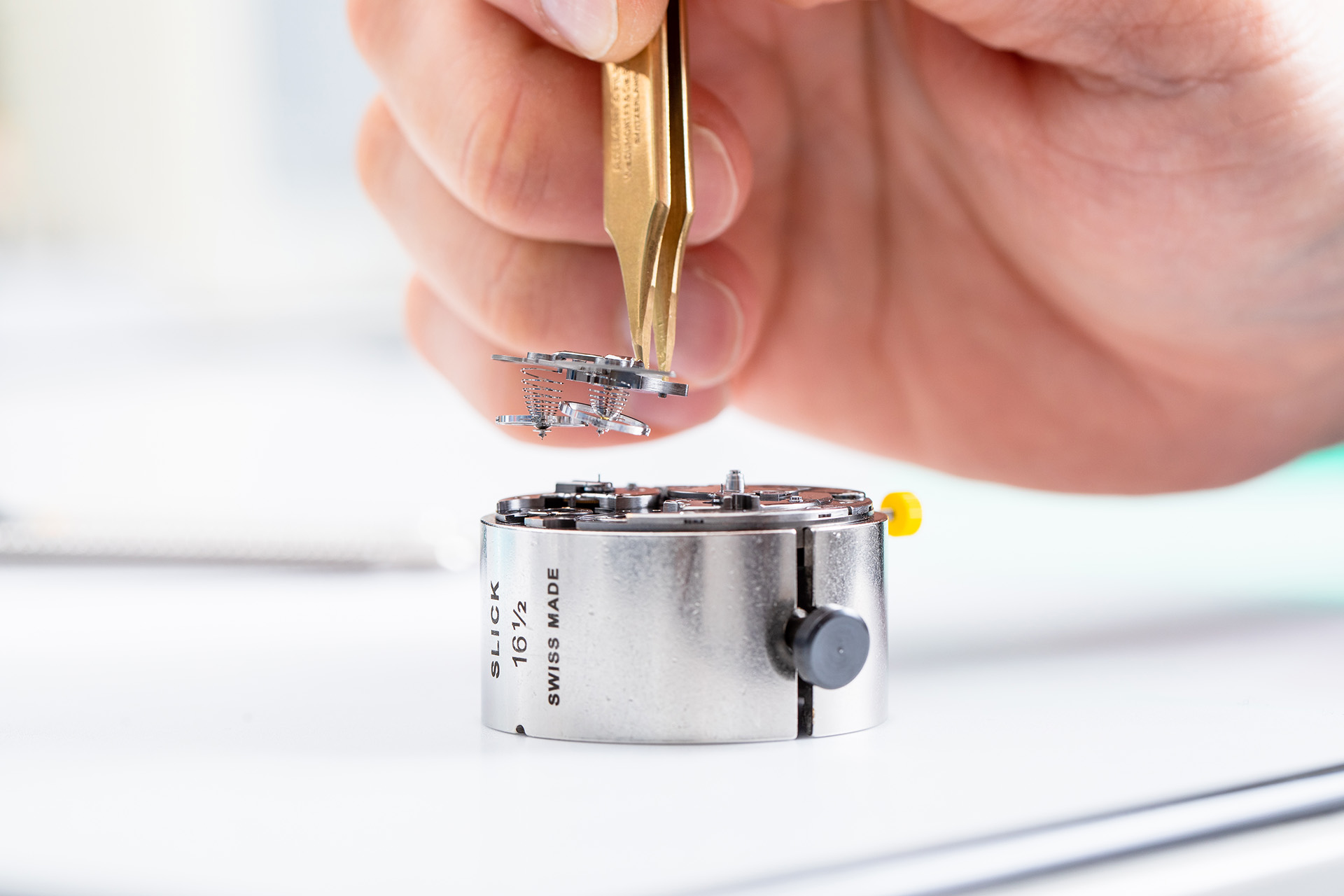
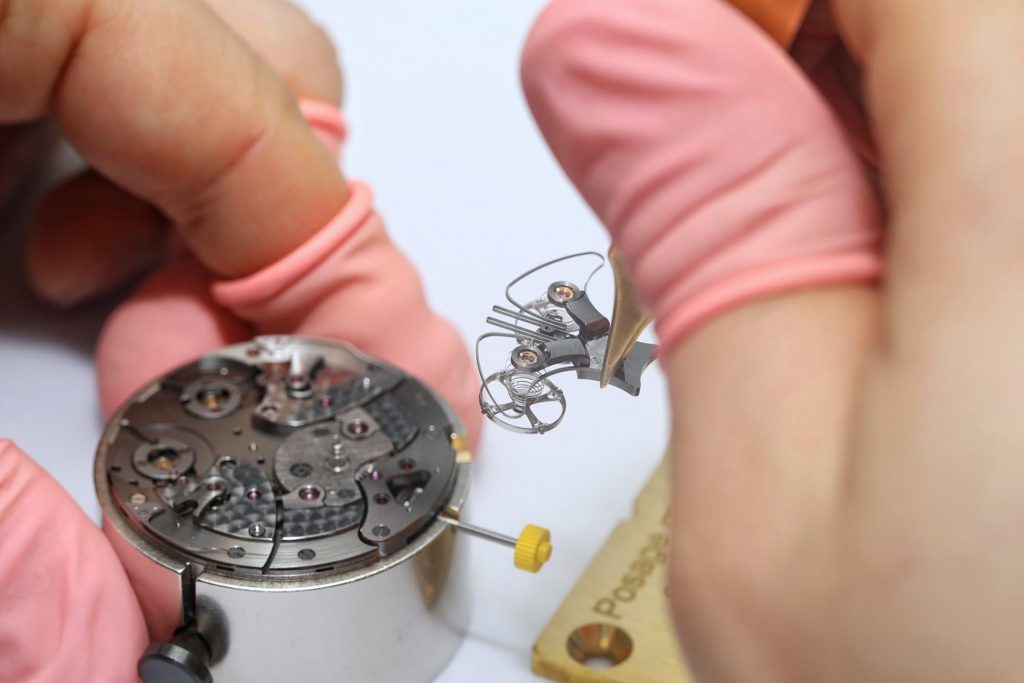
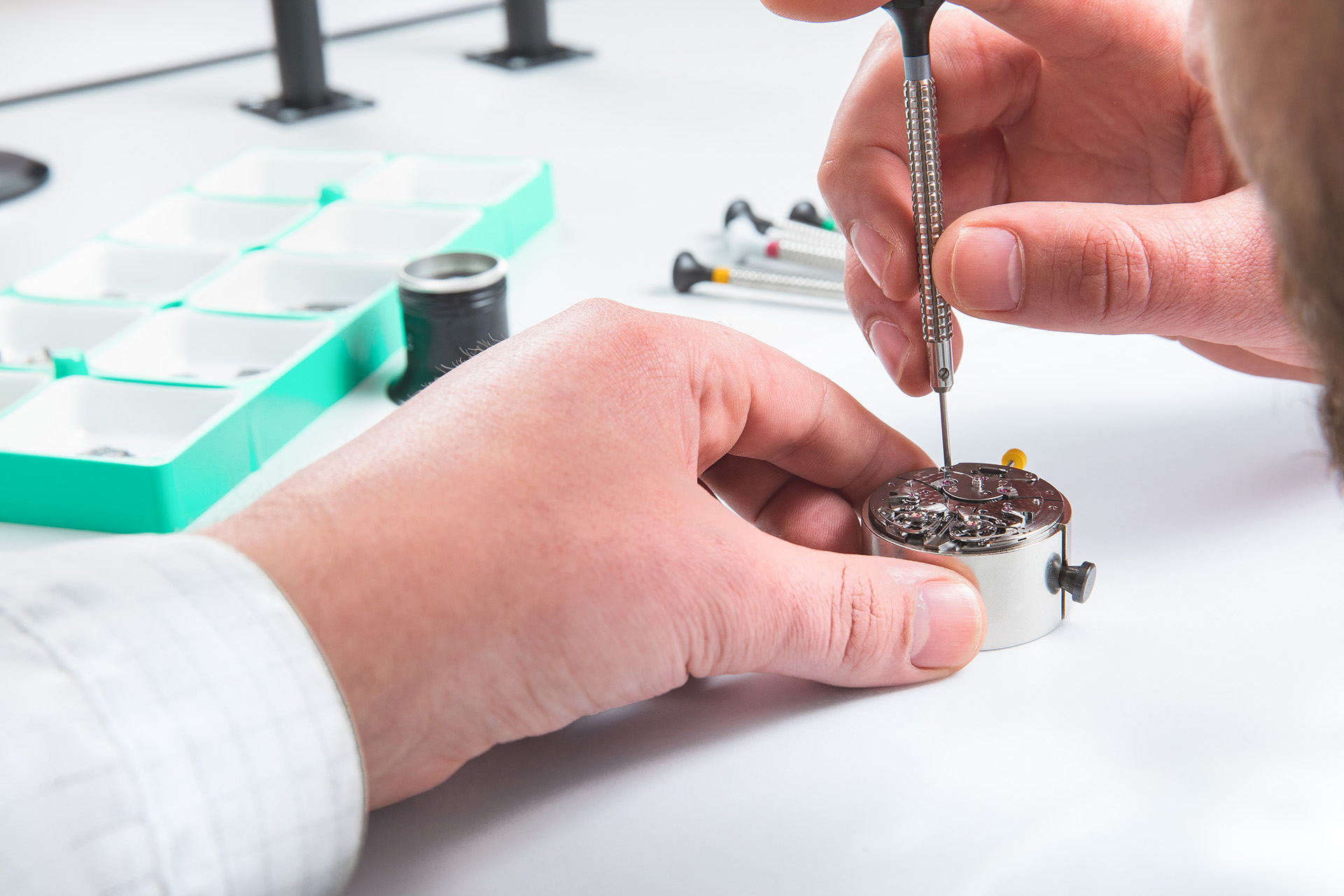
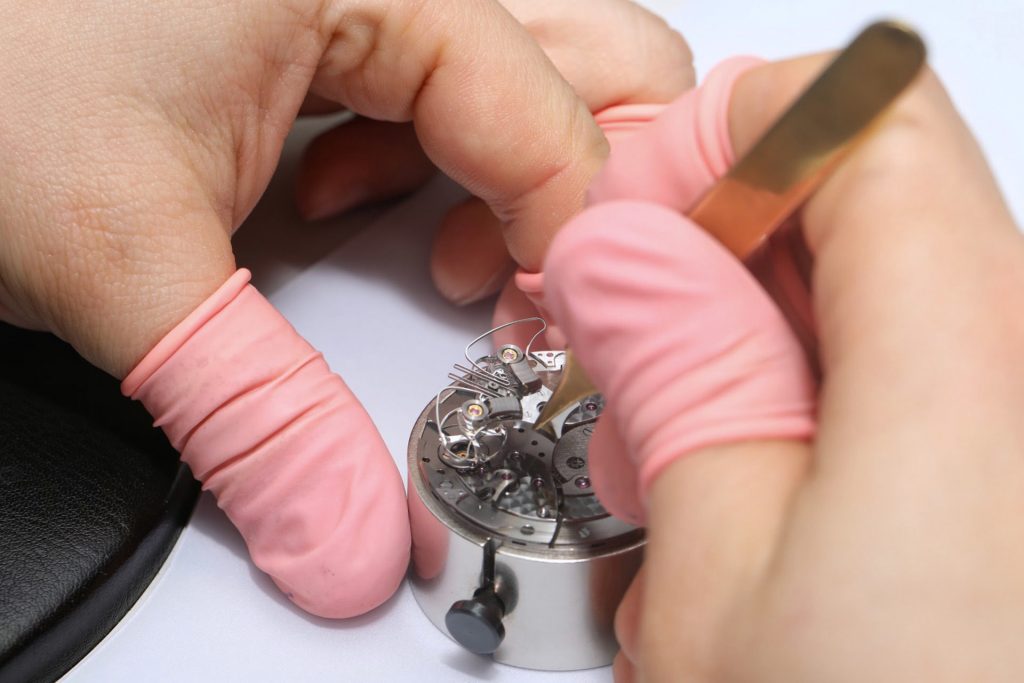

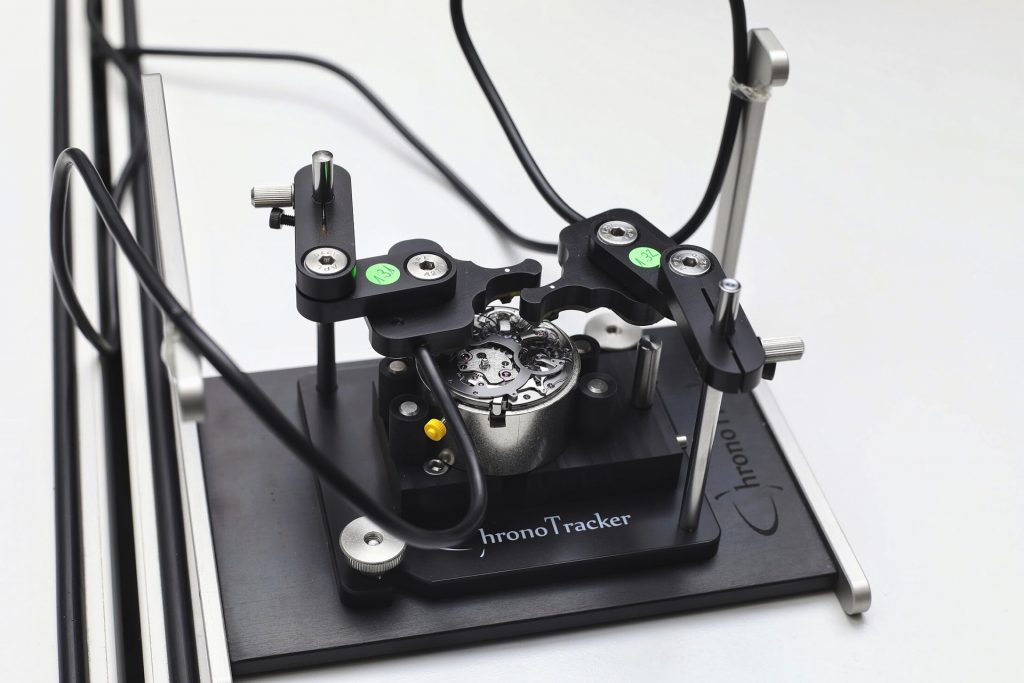
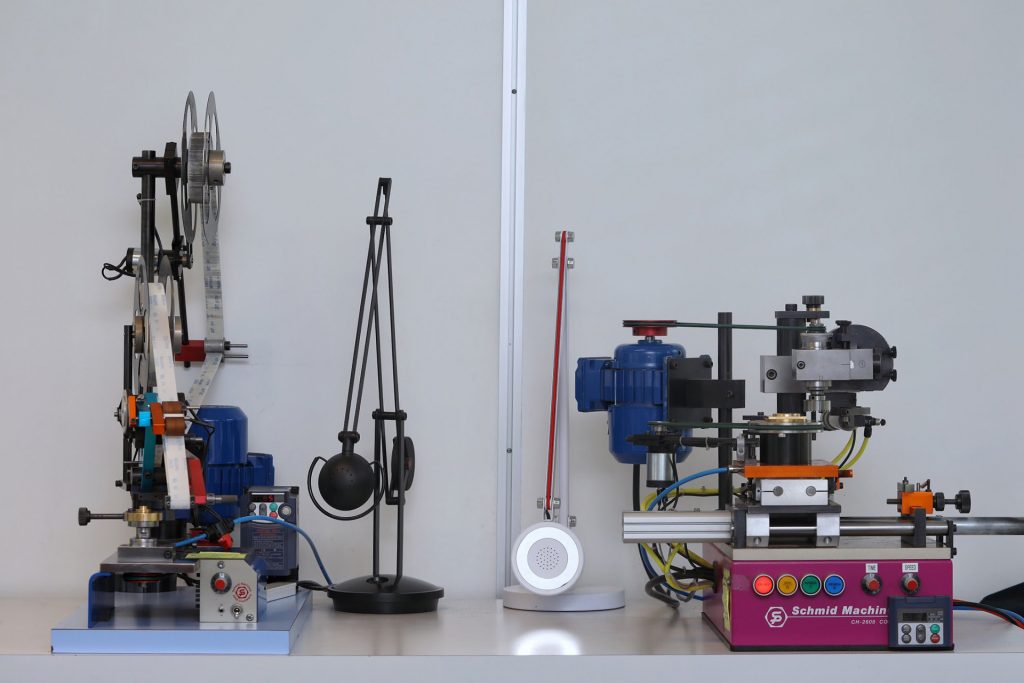